ABB, together with other leading automation companies and international standards organizations, has developed a field-level Ethernet connection for hazardous areas in the process industry – the Ethernet Advanced Physical Layer. By expanding its application to OPC UA based fusion networks, it helps the industry cross the boundaries between IT/OT and achieve seamless integration from the field to the cloud.With the rapid development of communication and network technology, process automation technology is undergoing continuous technological iteration and application transformation. Data and transmission have become an important driving force for the advancement of the industrial Internet of Things.
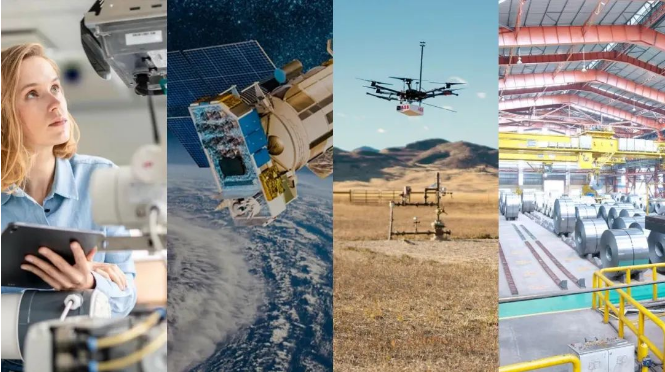
The Development History of Data Transmission Technology
In the early days, the main method of measuring process values was to connect field instruments to a distributed control system (DCS), which relied on simple wiring to convert analog measurements into 4-20 mA analog signals. Afterwards, HART technology introduced digital communication on the basis of analog signals, thereby maintaining the simplicity advantage of traditional wiring. Despite being digitized, bandwidth and communication speed are still extremely low.
The fully digital serial fieldbus technology introduced in the 1990s became the preferred technology in the early years of the 21st century. Due to increased bandwidth, this technology requires a gateway and is too complex in engineering, operation, and maintenance to truly meet the requirements of process industry suppliers.
To achieve a fully digital future, the process industry needs a technology with Ethernet level bandwidth and communication speed that is easy to design, operate, and maintain, while also expanding to on-site devices and operating in hazardous areas.
Expanding Ethernet to the Process Industry
Ethernet has become a widely recognized wired digital technology standard in many industries due to its high bandwidth and speed, with a complete set of standardized tools for installation, deployment, troubleshooting, and diagnosis. However, the application of Ethernet in the process industry is relatively limited. There are two prominent reasons: traditional communication technology dominates due to its simplicity and cost-effectiveness; There are hazardous conditions in many process industrial environments.
In 2015, with the support of 12 leading automation companies such as ABB and 4 international standard development organizations, the Advanced Physical Layer (APL) project was launched. In 2018, they determined that any sustainable solution should be fully compatible, meet the IEEE 802.3cg Ethernet standard, and meet specific standards, including dual wire cables, long cable lines, the same cable for power supply and communication, and support all explosion-proof technologies, including intrinsic safety Easy installation, etc.Ethernet Advanced Physical Layer (Ethernet-APL) is the result of nearly a decade of expanding Ethernet to the field. The network structure of Ethernet-APL is simple, does not require protocol conversion, and has high compatibility and ease of use. It has a speed of 10 Mbps and combines the simplicity of 4 to 20 mA signal connection with Ethernet level bandwidth suitable for instrument communication and multi-protocol support. By connecting to widely distributed dual wire loop powered field instruments in hazardous areas, Ethernet APL can improve communication performance without compromising safety.
This milestone technology, due to its characteristics of high-speed, safety, compatibility, and interoperability, has groundbreaking catered to the new needs of the Industry 4.0 era. Many experts in academia and industry are optimistic about its broad application prospects.
Peng Yu
Technical Advisor, Shanghai Institute of Industrial Automation Instrumentation
Honorary Chairman of PLCopen China Organization
In the wired and wireless physical layers of Ethernet, the Advanced Physical Layer (APL) is undoubtedly the most suitable underlying communication technology for the future process industry. It successfully solves the problem of using a pair of twisted pairs to transmit Ethernet signals over long distances, while supplying power to on-site instruments and actuators, and also ensuring the intrinsic safety of working in various hazardous areas. Its sufficient bandwidth and full duplex/bidirectional communication ensure that automation instruments and devices can receive control commands in real-time, while also transmitting process parameters, maintenance data, and engineering data to the control system, upper level maintenance and optimization system. In short, APL enables the collection, evaluation, and correlation of data from different sources and types, which is a powerful guarantee for the underlying data of digital transformation in the process industry.
With reliable on-site real-time data, the digital twin of process operation optimization and predictive maintenance can be implemented; With reliable communication technology, it is convenient and feasible to use centralized systems for remote monitoring of process facilities distributed in different geographical locations; Once a sufficiently large time series data pool is collected, the correlation between device failures and other events can be identified by human experts or artificial intelligence analysis, enabling predictive maintenance and other efficiency. In addition, aggregating data from processes, engineering, and maintenance throughout the entire lifecycle of assets can uncover in-depth insights that help further optimize production.
Dai Wenbin
Professor, School of Electronic Information and Electrical Engineering, Shanghai Jiao Tong University
Ethernet-APL provides an economical and effective upgrade path for existing process control systems. On the basis of significantly improving the transmission rate of instruments, it also provides protection measures for safe operation, extending the industrial internet to the process control site through Ethernet. It provides standardized communication protocols for achieving a network from on-site instruments to the cloud, with huge market potential and promotion value, It will definitely become the mainstream of the market in the near future.
Ethernet-APL is compatible with various leading industrial communication protocols, including PROFINET, Modbus TCP, and the increasingly popular OPC UA. ABB combines OPC UA technology with Ethernet-APL, making this universally applicable modern communication protocol applicable to field devices. The semantic and information model it brings eliminates the need for descriptive text, which helps bridge the gap between operational technology (OT) and information technology (IT).
Liu Dan
Beijing Institute of Mechanical Industry Instruments and Meters Comprehensive Economic and Technological Research
Deputy Chief Engineer
Ethernet-APL follows the IEEE802.3cg standard and uses a single pair of cables to carry the Ethernet standard. It can provide a bandwidth of 10Mbps over a length of 1000 meters, complies with the IEC TS 60079-47 standard, meets the intrinsic safety requirements of industrial sites, and has complete consistency testing specifications. Industrial Ethernet protocols such as PROFINET, HART-IP, EtherNet/IP, and OPC UA can directly use APL, which is of epoch-making significance for achieving “one network to the end” across the entire factory, especially for the process industry.
Song Huazhen
Technical Communication Manager, ABB Baikalai Industrial Automation (China) Co., Ltd
Member of SAC/TC124/SC4 Fieldbus Subcommittee
Communication is about connectivity, collaboration, and engineering efficiency. Ethernet-APL is an advanced physical layer standard and has been selected as the OPC UA FX field level communication protocol, enabling field instruments, sensors, analytical instruments, etc. to connect from the field to the cloud using widely used Ethernet technology. For users, it can achieve more global and efficient analysis and optimization, and improve the efficiency of factory operations. For instrument equipment manufacturers, it reduces development costs, while for engineering integrators, Ethernet-APL will reduce engineering implementation costs and provide flexible upgrade and expansion opportunities.
Zhang Yu
Chief Representative of OPC Foundation in China
Ethernet-APL is the main component of the OPC UA FX field level standard. It provides low-cost and more robust physical connections for the process industry. Combined with the OPC UA specification, factory data can be efficiently transmitted from the field to the cloud through various existing Ethernet software and hardware resources.
As the fifth generation advanced data communication technology for process industry factory sites, Ethernet advanced physical layer technology has opened a new era, achieving fast, secure, and reliable communication from the site to the entire enterprise and cloud, elevating digital connectivity to a new level, and effectively promoting industry towards a future of digital intelligence.
I don’t think the title of your article matches the content lol. Just kidding, mainly because I had some doubts after reading the article.
Your article helped me a lot, is there any more related content? Thanks!