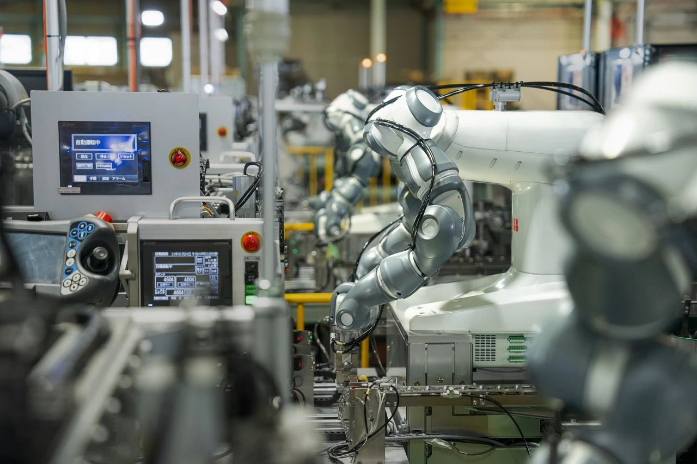
ABB YuMi ® Collaborative robots assist SUS Corporation in achieving production return and addressing labor shortages in Japan
Double arm YuMi effectively reduces assembly time, improves production efficiency by 20%, and enhances production flexibility
SUS uses ABB’s RobotStudio ® Efficient development automation solution for offline programming simulation software
YuMi from ABB ® Collaborative robots help Japanese SUS company drive production backflow and address the challenges posed by labor shortages. The company is a major supplier of aluminum frames and die cast aluminum parts for the automotive and other manufacturing industries.
Joerg Reger, Global Head of ABB Robotics Automotive Business Unit, stated that production backflow is seen as an effective way to address supply chain resilience and uncertainty, but it may also make production more complex. To address these issues, we offer a range of flexible automation solutions. We are pleased to see that SUS company is benefiting from it, achieving significant time savings, improving production efficiency, and quickly adapting to supply chain changes. This further proves that the application of automation technology is widespread and not limited to large vehicle factories.
In recent years, global supply chains have been frequently affected by fluctuations. In order to better control delivery times and enhance production flexibility, SUS company has decided to return to local production in Shizuoka, Japan. However, due to the production process itself containing a large number of repetitive and monotonous manual operations, coupled with the increasingly severe labor shortage, companies find it difficult to recruit and retain enough workers to meet production needs.
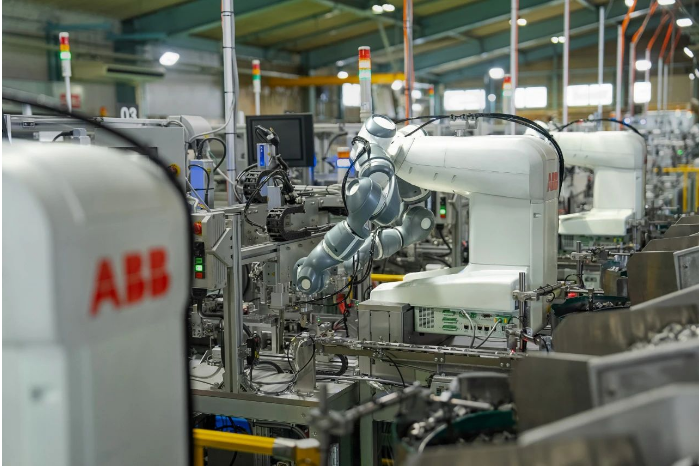
To address this issue, SUS company has introduced a series of YuMi dual arm collaborative robots. YuMi not only shortens assembly time and improves production efficiency by 20%, but also provides the much-needed flexibility to cope with demand fluctuations. The investment cost is expected to be recovered within two years.
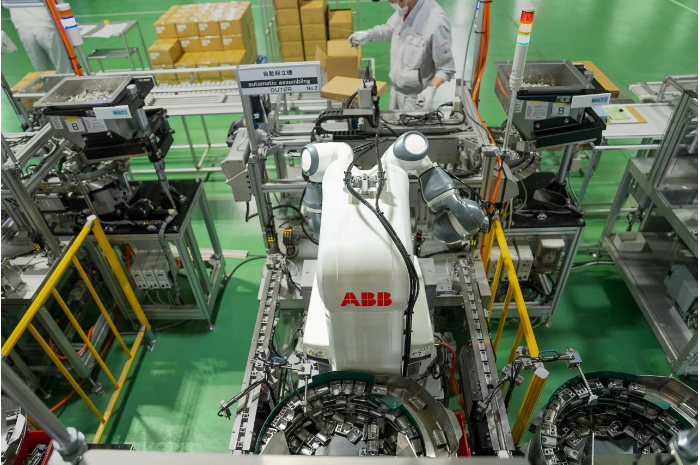
Through ABB’s RobotStudio ® Offline programming simulation software, the solution used by SUS can be designed in a virtual environment, optimized for operational processes, and then deployed in the real world. Through simulation, it was also verified that the YuMi dual arm collaborative robot’s single arm seven axis motion mode can accurately complete the complex twisting actions required during the assembly process. In addition, RobotStudio can accurately calculate the achievable output, helping SUS company make wise investment decisions. At present, SUS company is researching the addition of more robot units for other products and exploring the possibility of achieving automation in other production processes.
Akihiro Taki, the manager of the die-casting team at SUS Shizuoka factory, said that robots have taken over monotonous and tedious work, allowing workers to be reassigned to more valuable tasks. In addition, the new system only requires a small number of workers to operate at night, reducing the required number of specialized assembly equipment from 11 to 5.

In a recent survey on the prospects of the automotive manufacturing industry, ABB found that nearly one-third (31%) of respondents identified labor shortage as one of the top three challenges, while up to 35% of respondents listed labor as the most concerning factor when it comes to cost increases.
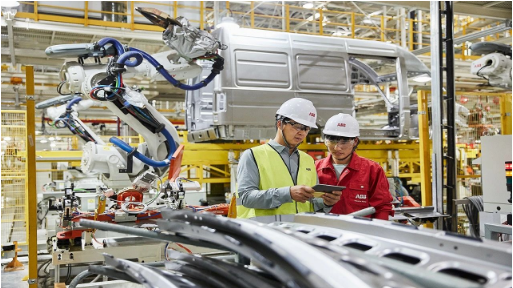
Recommended models for warehouse spare parts:
AMAT 0100-90952
KONGSBERG CRP330952
WOODWARD 8440-1952
wall mounted battery home energy storage power wall battery
BENTLY 330130-080-00-00 Standard Extension Cable
PPA322B HIEE300016R2 HIEE400235R1
vurcazkircazpatliycaz.yVtDbKJX9GRv
Dear friend, may I ask if there is anything I can help you with?
vurucuteamgeldi.ttbK4Ige4QT4
Dear friend, what can I do for you?
Dear friend, thank you for your recognition. I will continue to work hard.
Your point of view caught my eye and was very interesting. Thanks. I have a question for you.