Koma has developed and deployed a large-scale automated production line for lemon hybrid DHT production
An end-to-end solution ensures an annual production capacity of 150000 units per production line, while controlling production pace for less than 2 minutes
This highly scalable system aims to reduce the production costs of future DHT product upgrades, demonstrating excellent adaptability and efficiency
Flexible and scalable production lines have customization capabilities to flexibly meet ever-changing market demands
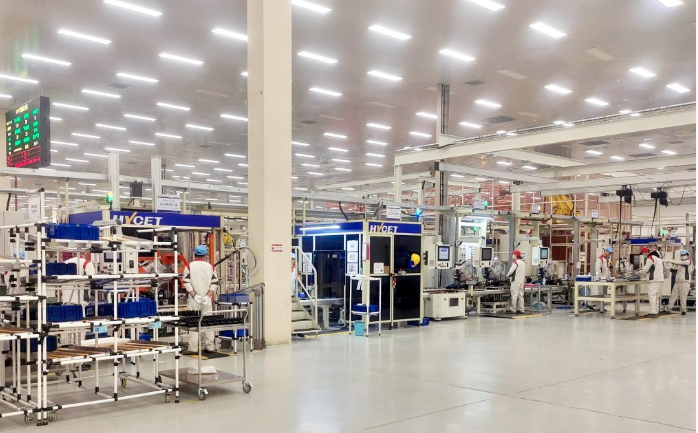
Koma has recently successfully designed and deployed a large-scale automated production line for Honeycomb Drive, a leading manufacturer of DHT technology under Great Wall Motors. This assembly line is specifically designed for the lemon hybrid DHT, a new generation transmission system that enables efficient power sharing between gasoline engines and motors. To achieve the goal of large-scale manufacturing, Koma’s end-to-end solution is equipped with 12 robots on each of the 6 production lines, ensuring an annual production capacity of 150000 units per production line and controlling the production pace for less than 2 minutes.
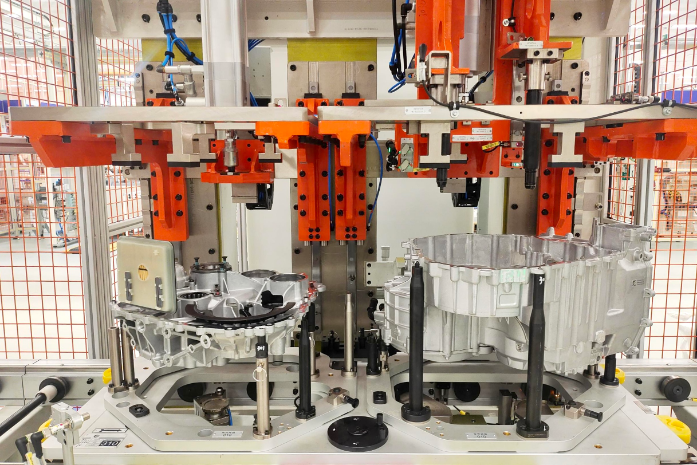
Koma has fully developed the required components within the project scope, including motor assembly lines, shaft assembly lines, main assembly lines, and assembly testing lines, covering the entire process assembly from components to the entire machine assembly line. This high-speed production solution not only meets the strict requirements of Honeycomb Drive for manufacturing accuracy and product quality, but also ensures better adaptability and efficiency, helping to reduce the production costs of future DHT product upgrades. The production line designed by Koma has significant flexibility and can be easily customized to meet different market demands.
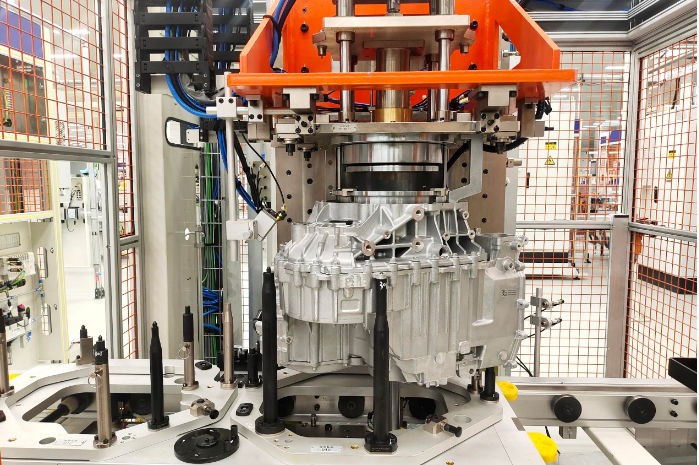
Koma also adopts a process integrated overall workstation design, ensuring the stability and product quality of the entire production line, and the equipment mobility rate is as high as 90%. Through MES (Manufacturing Execution System), Honeycomb Drive can optimize the management and scheduling of production lines, achieve continuous monitoring of key process parameters (such as force and displacement), ensure quality control of the entire production process, and support traceability of subsequent data.
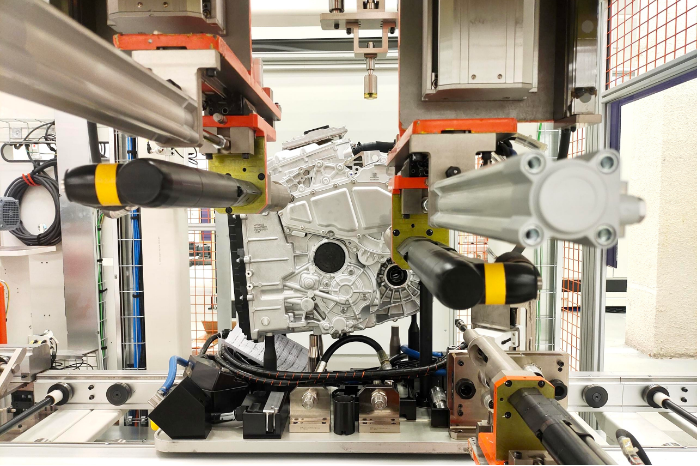
“Honeycomb Drive DHT technology showcases cutting-edge innovation in the field of hybrid vehicles, injecting excellent performance into Great Wall Lemon DHT products. As a partner in our new technology, Koma’s reliable design and engineering capabilities confirm its outstanding position in this field,” said Wu Hongchao, Vice President of Honeycomb Yichuang Technology Co., Ltd. “During the project execution phase, despite being affected by the pandemic multiple times, Koma still strictly delivered according to plan and maintained consistent manufacturing quality. This stability is crucial for our production process, enabling us to meet market demand and maintain efficient production.”
“This project is an excellent opportunity for Coma to collaborate with leading companies in the field of hybrid transmission technology,” explained Yuan Yingjun, the head of Coma’s Asia Pacific region, “By prioritizing flexibility, efficiency, and absolute quality in our manufacturing philosophy, Koma has designed a 100% error proof production process to assist Honeycomb Drive in reducing costs and increasing efficiency, achieving large-scale manufacturing goals. Our competitiveness in the field of electric mobility stems from our long-term experience in traditional engines and power systems, making Koma a global leader in new energy vehicle solutions.”
Koma is committed to the development of electric drive technology, continuously expanding its technology portfolio to meet the growing demand for electric vehicle applications. The company focuses on designing, manufacturing, and integrating flexible, modular, reconfigurable, and scalable automation solutions, covering stator assembly systems, rotor assembly systems, electric drive assembly systems, electronic control assembly systems, and electric drive system housing machining solutions. At the same time, Koma focuses on developing automated manufacturing systems that cover battery cells, modules, and various battery packs, providing solutions for different stages of battery production, including battery formation technology. Thanks to its comprehensive product portfolio, technological strength, and cutting-edge technology, Koma is able to provide a one-stop solution from prototype design and pre manufacturing to large-scale production and even the recycling and disposal of discarded batteries.
Based on the forefront of innovation in the fields of automation and electrification, Koma is empowering global customers in all aspects, helping them improve and upgrade through advanced technology, process research and development, and digital tools. The company focuses on large-scale electrification in the automotive market, fully supporting customers in developing market leading new energy vehicles and providing advanced solutions for the future.
Recommended warehouse spare parts:
HIMA F35
HIMA H4135A 992413560
HIMA H4135 992413502
HIMA F8620/11
HIMA BV7032-0,5
HIMA BV7046-4
HIMA EABT3 B9302 997009302
HIMA ELOPII
HIMA F3 AIO 8/4 01
HIMA F3 DIO 20/8 02
vurcazkircazpatliycaz.Ekf0x4qyOfdJ
Dear friend, may I ask if there is anything I can help you with?
vurucuteamgeldi.YSIaCxlAyiEB
Dear friend, what can I do for you?
Some genuinely nice and utilitarian info on this website, also I conceive the design has got good features.
It is in reality a nice and useful piece of info. I’m satisfied that you shared this helpful information with us. Please stay us informed like this. Thank you for sharing.
You are my inspiration , I have few blogs and sometimes run out from to post : (.
Do you mind if I quote a couple of your posts as long as I provide credit and sources back to your blog? My blog site is in the very same area of interest as yours and my users would definitely benefit from some of the information you present here. Please let me know if this okay with you. Appreciate it!
Way cool, some valid points! I appreciate you making this article available, the rest of the site is also high quality. Have a fun.
Good morning, dear friend! May your day be filled with sunshine and laughter, with each step taken firmly and powerfully. Wishing you all your wishes come true, all the best, good morning and good luck!
Thank you for your recognition. I will work even harder. If you need to learn more, please visit:
https://www.weikunfadacai1.com/product/abb-gfd563a102/
Hi, i think that i saw you visited my website thus i came to “return the favor”.I’m trying to find things to improve my site!I suppose its ok to use some of your ideas!!
Dear friend, thank you for your recognition. If you need to learn more, please visit:
https://www.weikunfadacai1.com/product/3bhe041576r3011-abb-excitation-system-central-processing-module-3bhe041576r3011/
F*ckin’ awesome things here. I am very glad to peer your post. Thanks a lot and i am taking a look forward to contact you. Will you kindly drop me a e-mail?
Dear friend, thank you for your recognition. If you need to learn more, please visit:
https://www.weikunfadacai1.com/product/ppd103801-3bhe020455r0001-ac800pec-system-excitation-controller-ppd103801/
excellent points altogether, you just won a emblem new reader. What would you suggest about your put up that you made some days in the past? Any positive?
Dear friend, hello. It’s great to receive your comment. If you need to know more, please visit:
https://www.weikunfadacai1.com/product-tag/power-module/
Good write-up, I¦m regular visitor of one¦s blog, maintain up the nice operate, and It’s going to be a regular visitor for a lengthy time.
I precisely desired to say thanks all over again. I’m not certain the things I would have implemented in the absence of the entire recommendations revealed by you over this situation. Previously it was an absolute daunting concern in my position, but considering the very expert technique you handled that forced me to jump for contentment. I am happy for your guidance and then trust you are aware of a great job that you are doing instructing many people by way of your blog. I am certain you haven’t met any of us.
Greetings from Ohio! I’m bored to tears at work so I decided to check out your site on my iphone during lunch break. I really like the info you provide here and can’t wait to take a look when I get home. I’m shocked at how fast your blog loaded on my mobile .. I’m not even using WIFI, just 3G .. Anyways, fantastic site!
I have recently started a website, the info you offer on this site has helped me greatly. Thanks for all of your time & work.
I don’t think the title of your article matches the content lol. Just kidding, mainly because I had some doubts after reading the article.
Can I simply say what a relief to find someone who really knows what theyre talking about on the internet. You definitely know how one can carry a problem to light and make it important. Extra folks need to read this and perceive this side of the story. I cant consider youre not more widespread since you undoubtedly have the gift.