Description
A 1756 GuardLogix® controller is a ControlLogix controller that also provides the ability to perform safety functions. You must use a primary safety controller and a safety partner to achieve up to SIL CL 3/PLe/Cat. 4. A major benefit of this system is that it is still one project, safety and standard together. The safety partner is a part of the system, is automatically configured, and requires no user setup. With the introduction of the GuardLogix 5580 controller, users can achieve up to SIL 2/PLd (Category 3) with a single controller and the use of the safety task and safety I/O. During development, safety and standard have the same rules. Multiple programmers, online editing, and forcing are allowed. Once the safety system is validated and the safety signature applied, safety memory is protected, the safety logic cannot be modified, and all safety functions operate with SIL integrity.
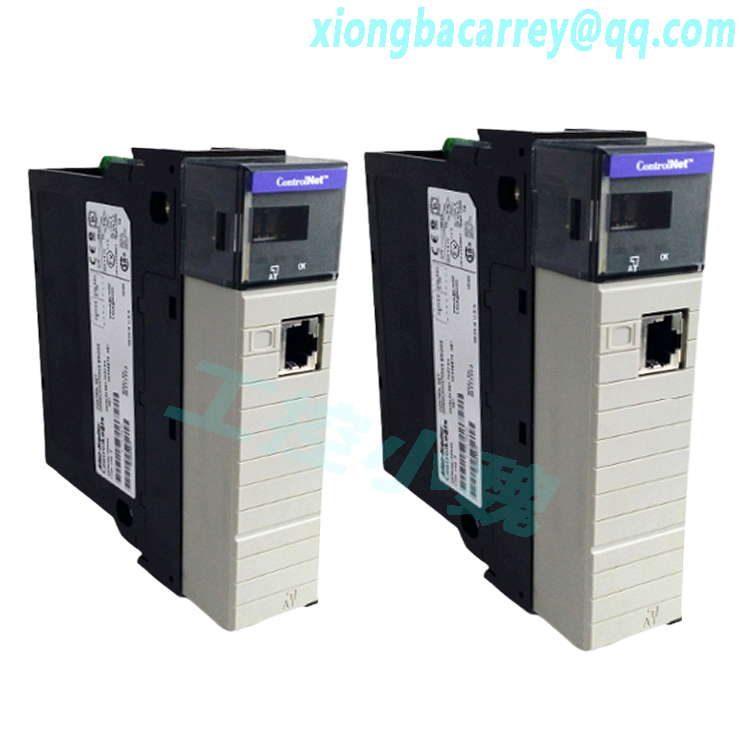
The 1756 GuardLogix-XT™ controllers function the same way as the traditional GuardLogix Controllers. The GuardLogix-XT controllers are conformal coated to add a layer of protection when exposed to harsh, corrosive environments. The GuardLogix-XT system can withstand temperature ranges from -25…+70 °C (-13…+158 °F). You must use a 1756-L73SXT primary controller with a 1756-L7SPXT safety partner. Customers who previously used the LXT chassis should now migrate to the K version of the chassis.
.jpg)
The 1756 Armor™ ControlLogix® and Armor™ GuardLogix® controllers extend the ControlLogix platform to the On-Machine™ space to put industrial control closer to the application, and sometimes onto the machine itself. The Armor GuardLogix controllers are certified for use in safety applications up to Safety Integrity Level (SIL) 3 and Performance Level PLe (Category 4), where the de-energized state is the safe state. Dual independent EtherNet/IP ports and Device Level Ring (DLR) capabilities provide resiliency from loss of network connections due to one connection failure. The controllers support the same environmental ratings and global certifications as the ControlLogix and GuardLogix controllers, but now provide Ingress Protection (IP67 and UL Type 4/4x) for dust and washdown protection. With so many hardware functions in one device, these controllers minimize cabinet hardware and simplify wiring layouts. The controllers do not require specialty tools or specialty personnel for component replacement. These features can help improve Mean Time to Repair (MTTR), simplify troubleshooting, and make system status readily available without having to open a cabinet or visit a control room.
ControlLogix Redundancy ControlLogix 5580 and ControlLogix 5570 controllers support controller redundancy. In a redundant controller system, you need these components: • Two 1756 chassis, each with the same of the following: – Number of slots – Modules in the same slots – Redundancy firmware revisions in each module – Approved module firmware revisions for use within ControlLogix Redundancy systems. • One 1756-RM2, 1756-RM2K, or 1756-RM2XT module per chassis that supports the following: – One or two ControlLogix controllers of the same family. ControlLogix 5580 controllers support redundancy with Studio 5000 Logix Designer application, version 33.00.02 or later. – For ControlLogix 5580 controllers, as many as seven EtherNet/IP communication modules. – For ControlLogix 5570 controllers, as many as seven ControlNet or EtherNet/IP communication modules in any combination. • One or two 1756-RMCx cables For information on the differences between ControlLogix 5580 and ControlLogix 5570 controllers, see Replacement Guidelines: Logix 5000 Controllers Reference Manual, Publication 1756-RM100.
.jpg)
1756 ControlLogix Batteries Each ControlLogix 5560 controller ships with a battery. The ControlLogix 5560 controllers have nonvolatile memory if you install a 1784-CF128 industrial CompactFlash card. With nonvolatile memory, the controller can be used without a battery. If you do not use a battery, current tag data remains in the state it was when the nonvolatile memory was saved. This table summarizes battery life, replacement battery compatibility, and recommendations for use of an externally-mounted battery assembly.
ControlLogix Controller and Memory Board Catalog Numbers 1756-L1, 1756-L1M1, 1756-L1M2, 1756-L1M3, 1756-L55, 1756-L55M12, 1756-L55M13, 1756-L55M14, 1756-L55M16, 1756-L55M22, 1756-L55M23, 1756-L55M24, 1756-L61, 1756-L62, 1756-L63, 1756-L64, 1756-L65, 1756-M1, 1756-M2, 1756-M3, 1756-M12, 1756-M13, 1756-M14, 1756-M16, 1756-M22, 1756-M23, 1756-M24, 1784-CF64, 1784-CF128
.jpg)
This equipment is intended for use in a Pollution Degree 2 industrial environment, in overvoltage Category II applications (as defined in IEC publication 60664-1), at altitudes up to 2000 m (6561 ft) without derating. This equipment is considered Group 1, Class A industrial equipment according to IEC/CISPR Publication 11. Without appropriate precautions, there may be potential difficulties ensuring electromagnetic compatibility in other environments due to conducted as well as radiated disturbance. This equipment is supplied as open-type equipment. It must be mounted within an enclosure that is suitably designed for those specific environmental conditions that will be present and appropriately designed to prevent personal injury resulting from accessibility to live parts. The enclosure must have suitable flame-retardant properties to prevent or minimize the spread of flame, complying with a flame spread rating of 5VA, V2, V1, V0 (or equivalent) if non-metallic. The interior of the enclosure must be accessible only by the use of a tool. Subsequent sections of this publication may contain additional information regarding specific enclosure type ratings that are required to comply with certain product safety certifications. In addition to this publication, see: • Industrial Automation Wiring and Grounding Guidelines, for additional installation requirements, Allen-Bradley publication 1770-4.1. • NEMA Standards publication 250 and IEC publication 60529, as applicable, for explanations of the degrees of protection provided by different types of enclosure.
Model recommendation:
Reviews
There are no reviews yet.