Description
Many products have not been listed yet. For more products, please contact us
If the product model is inconsistent with the displayed image, the model shall prevail. Please contact us for specific product images, and we will arrange for photos to be taken and confirmed in the warehouse
We have 16 shared warehouses worldwide, so sometimes it may take several hours to accurately return to you. We apologize for any inconvenience caused. Of course, we will respond to your concerns as soon as possible.
Ship control system controlled by joystick
technical field
The present invention relates to a control system for a ship’s joystick, and specifically to a joystick control controller with an input loop and an actuator loop. The input loop converts user joystick control inputs into corresponding ship control commands, and the actuator loop converts ship control commands into corresponding ship controller and propulsion system command inputs.
Background technology
Seagoing vessels of various sizes and functions require the ability to precisely control navigation in narrow or restricted waters, including and ranging from yachts, fishing boats and workboats, cruise ships, and ferries visiting small ports, fjords, estuaries, or other interesting narrow areas to larger vessels, such as tugboats, various port vessels, survey boats, salvage boats, supply boats, and offshore work boats, The larger vessels find themselves in actually narrow waters due to their size and/or draft, such as larger cruise or passenger ships, oil tankers, cargo ships, drilling rigs, and platforms. These ships often require the ability for precise and controllable translational motion, namely linear motion, as well as precise and controllable rotation around a fixed axis extending vertically through the centerline of the ship.https://www.weikunfadacai1.com/
These requirements are typically met through manipulation and propulsion systems that include traditional propulsion and navigation systems, which consist of one or more steerable rudders and one or more independently controllable thrusters combined with the manipulation system. The manipulation system includes one or more fixed or steerable boosters, such as pump or ducted thrusters.
However, this combined propulsion and maneuvering system suffers from many drawbacks and problems, the most common and persistent of which is that when controlled through this system, each system is usually unique in terms of its own characteristics and the maneuvering characteristics of the ship itself. Therefore, each person who is going to lead a ship equipped with this propulsion and control system needs to independently learn and widely practice the ship and the propulsion and control system, in order to master the propulsion and control system and the individual and unique maneuvering characteristics of the ship to the extent necessary for safe navigation of the ship. These issues are complex because each propulsion system, such as the main engine, rudder, and bow and stern boosters, has its own independent user interface. In addition, the knowledge and experience gained by personnel regarding a ship and its propulsion and control systems can only be partially transmitted to different ships and propulsion and control systems in the best case, making it necessary to roughly relearn each new ship and propulsion and control system from scratch.
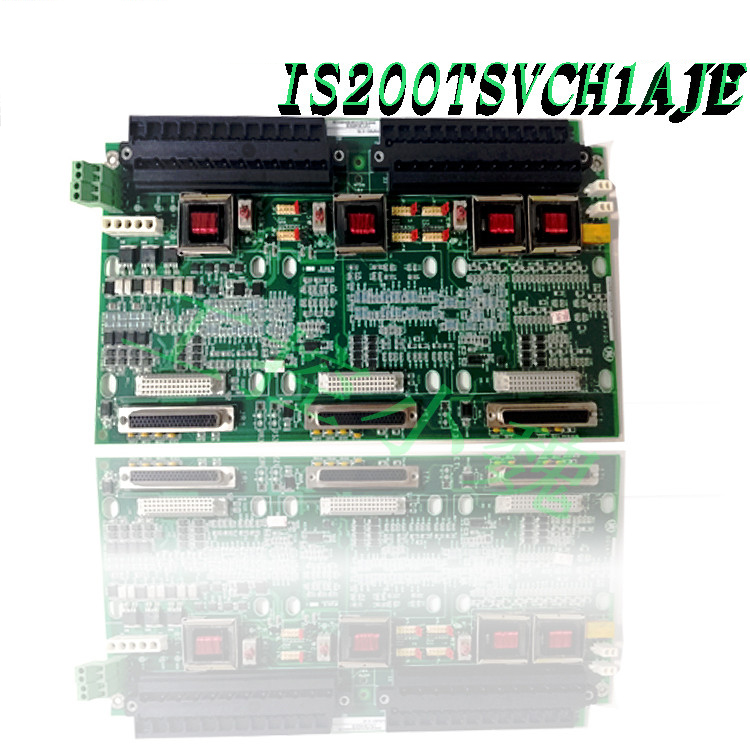
It must also be noted that the characteristics of the ship and its propulsion and control systems must be determined separately, such as when the ship and propulsion and control systems are initially built and delivered for use, or when they are added to existing ships. This process must be repeated when there are any significant changes or modifications to the ship or propulsion and control system, which may affect the maneuvering characteristics of the ship or propulsion and control system.(https://www.weikunfadacai1.com/)
However, determining the maneuvering characteristics of new or modified ships or propulsion and control systems is a lengthy and expensive process, such as conducting “mooring column” tests for automatic control systems. In the mooring column test for automatic control systems, the ship is moored to a fixed mooring column device, and the force applied by the ship to the mooring equipment is measured during training of the ship and propulsion and control systems throughout their entire range of maneuvering and propulsion capabilities. Generally, based on the measurement and physical parameters of the ship and propulsion and control systems, such as ship size, wind influence, mass, etc., the calculated response of the ship is used to calculate the possible maneuvering characteristics of the ship and propulsion and control systems.
-1.jpg)
However, it is evident that the calculated maneuvering characteristics of the ship and propulsion and control systems may not be accurate or even sufficient to represent the actual maneuvering characteristics of the ship and propulsion and control systems, especially under actual operating conditions such as wind and water flow effects or ship loading effects. Therefore, prior to obtaining sufficient practical experience with the ship and propulsion and maneuvering systems under actual operating conditions, the understanding of the actual maneuvering characteristics of the ship and propulsion and maneuvering systems did not reach the expected level of confidence. It will also be recognized that the personnel expected to navigate the vessel cannot understand the maneuvering characteristics of the vessel or propulsion and control systems based on the calculated characteristics, and for each vessel and propulsion and control system, they must learn these matters again through practical experience with the vessel and propulsion and control systems.
The present invention provides a solution to these and related problems of the prior art.
summary of the invention
The present invention is dedicated to a marine propulsion and steering system for ships, which has multiple operating modes and includes a ship propulsion system. The ship propulsion system includes an axial propulsion system, a maneuvering propulsion system, and a maneuvering system. The axial propulsion system includes at least one engine for controlling the axial motion of the ship, and the maneuvering propulsion system includes at least one controllable booster, The at least one controllable booster is used to control the rotational and translational motion of the ship.
The control system comprises at least one navigator controllable joystick and a control processor, wherein at least one navigator controllable joystick is used to generate propulsion and control inputs representing the expected ship motion of the navigator, and the control processor comprises an input loop controller and an actuator loop controller, wherein the input loop controller and actuator loop controller respond to the control inputs of the navigator joystick, Used to generate corresponding control outputs to at least one booster and to at least one engine, in order to control the translational and rotational motion of the ship according to the control input of the joystick.
The input loop controller responds to the joystick control input to generate control commands representing the amplitude and direction of the ship’s expected force, while the actuator loop controller responds to control commands from the input loop controller to generate corresponding ship control commands to the ship’s propulsion system, thereby generating propulsion and control forces to cause the ship to move according to the joystick input commands.
In addition, the present invention is dedicated to a method for controlling a ship propulsion system, which includes a joystick control, an axial propulsion system, and a maneuvering propulsion system. In the joystick control, the movement of the joystick around the axis of motion of the joystick provides corresponding motion control instructions to the ship propulsion system, The axial propulsion system comprises at least one of a first engine for controlling the axial motion of a ship, a rudder for controlling the direction of the ship’s motion, and a second engine for controlling the axial and directional motion of the ship. The maneuvering propulsion system comprises at least one controllable and/or controllable booster for controlling the rotational and translational motion of the ship.
According to the present invention, the operator selects one operating mode from the normal operating mode, the holding position operating mode, the holding position operating mode, and a combination of holding position and holding position operating modes. When in normal operating mode, all heading, axial motion, rotational motion, and lateral motion of the ship are controlled by the control lever input and controlled through the corresponding control lever input. When in the maintain azimuth operation mode, the system maintains the current azimuth of the ship constant and controls the axial and lateral movements of the ship through corresponding joystick inputs. When in the hold position operation mode, the system maintains the current ship position constant at the best capacity of the ship actuator, and when in the combined hold position and hold position operation mode, the system maintains the current ship position and position constant.
-1.jpg)
In another implementation of a method for controlling a ship propulsion system, the system comprises at least one of a basic propulsion operation mode, a maneuvering operation mode, and a driving operation mode. In this basic propulsion operation mode, the ship’s axial motion command is generated based on the corresponding motion of the control lever, while the ship’s rotation command is generated based on the corresponding rotation motion of the control lever. The system enters the control operation mode through the lateral motion command of the control lever, or when the motion of the generated axial motion command of the control lever exceeds the set point of the drive mode, the command system enters the drive operation mode. In the maneuvering operation mode, the ship’s lateral motion command is generated through the corresponding lateral motion of the control lever, while the ship’s axial motion command is generated through the corresponding motion of the control lever beyond the set point of the driving mode. In the driving operation mode, the ship’s axial motion command is generated through the corresponding motion of the control lever, while the rudder steering command and at least one of the first and second engine steering commands are generated based on the corresponding lateral motion of the control lever.
The term “steerable” used in conjunction with boosters refers to the ability of boosters to generate steering forces in at least two opposite directions.
Recommended warehouse spare parts:
Reviews
There are no reviews yet.