The era of bundled automation will become history.
Based on the decoupling of automation software and hardware, users can deploy the required automation functions on any standard compliant platform. In this way, enterprises can be guided by their own business needs, maximize the technological value of the new generation of automation, make the best decisions to meet the constantly changing consumer needs, and better transition to Industry 4.0 and move towards a digital future.
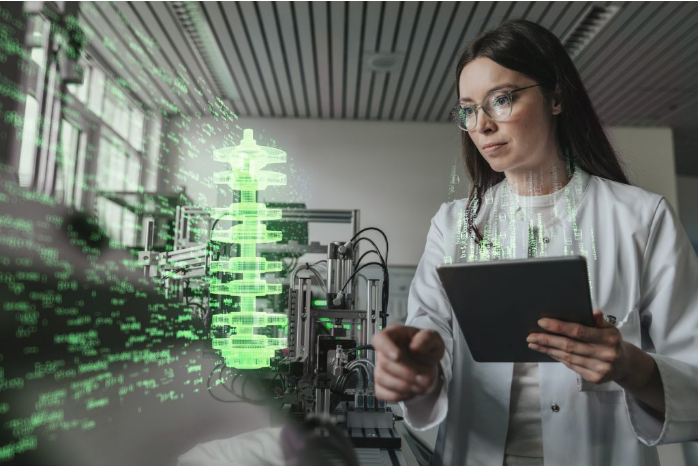
Relying on virtualization technology, leading a new height of industrial automation
On the basis of software and hardware decoupling, new virtualization technology has been widely applied in the industrial field, promoting the transformation and upgrading of traditional automation paradigms, and further improving the overall efficiency of enterprises.
In traditional IT concepts, “virtualization” is often used to describe the situation of setting up multiple virtual machines (VMs) on a single server. When applied in the field of industrial automation, although this technology encompasses multiple meanings, its premise is similar – to virtualize physical entities.
Regarding this, Ali Haj Fraj, Senior Vice President of Schneider Electric Global and Head of Industrial Automation Digital Factory, believes that “people have achieved digital upgrades in industrial process execution by combining hardware and software. In this process, by further leveraging the powerful functions of software, the value of virtualization technology will be maximized.”
Software+Digital Twin, Helping Enterprises Governance with “Virtual” and “Real”
By introducing digital twin modeling technology into the software, users can build digital twins of real assets in the virtual world, achieving “virtual real consistency” in operational management. Taking the manufacturing industry as an example, the EcoStruxure Machine Expert Twin (EMET) software from Schneider Electric can help machine manufacturers transform the “waterfall” physical hardware development process into an “agile” development process: by performing “drag and drop” operations in a predefined object directory, manufacturers can first design, optimize, test, and validate the digital model of machine solutions in a virtualized environment, and then proceed with actual development and debugging. As a result, users will no longer need to undergo physical hardware experiments to achieve optimization results. Compared to traditional development methods, this will save companies up to 50% of their time to market and 60% of their debugging time, thereby significantly improving overall efficiency.
Software PLC+Industrial PC enhances enterprise flexibility and agility
One of the core applications in industrial automation, programmable logic controllers (PLCs), can be transformed into software PLCs by combining virtualization technology. The virtual controller of Schneider Electric EcoStruxure open automation platform is a hardware independent, software based PLC that can run on any Windows or Linux server, industrial PC (iPC, industrial computer), or microcomputer, without being bound by supplier restrictions. This virtual controller supports multiple instances to be installed, configured, deployed, and maintained independently of each other at the same time and on the same hardware. It can also adjust and optimize the production process without stopping the production line, thereby minimizing downtime and reducing costs, helping enterprises better respond to dynamic and changing consumer demands and market environments, and improving their flexibility and agility.
In addition, the Schneider Electric Harmony iPC (formerly known as Magelis iPC) adopts a reinforced design, which has functions such as expanding temperature range and compatibility with industrial protocols, and can adapt to common harsh environments in production and manufacturing. As a terminal that integrates visualization and control, Harmony iPC has strong functionality and specificity, and is also a professional tool for industrial users to run software PLCs, machines, and factory control systems.
Using software to create reusable projects and strengthen core competitiveness
EcoStruxure, an open automation platform based on software defined automation, with built-in intelligent design and engineering functions, can quickly replicate and promote the process or technical application of any project to other fields. Taking carbon capture projects as an example, enterprises often find it difficult to achieve large-scale and replicable expansion of single regional projects. The reason for this is that the carbon capture process requires a highly flexible and efficient control system with the ability to scale as needed. As one of the pioneers in the field of algal carbon capture technology, Brilliant Planet has achieved many remarkable results with the powerful functions of Schneider Electric’s EcoStruxure open automation platform. Not only has it shortened the integration and testing time of control software for various project points, but it has also established a customizable and scalable system based on standardized application programs. At the same time, it has combined the AVEVA system platform and AVEVA Insight to achieve comprehensive visual management and control of the system operation.
“To achieve rapid and large-scale expansion of carbon capture projects, the ability to apply modularity and standardization is essential.” Adam Taylor, CEO of Brilliant Planet, said, “A solution based on Schneider Electric’s EcoStruxure open automation platform can help us replicate, transplant, and apply control systems for various projects, improve resource management capabilities and utilization efficiency. In the future, we hope to further promote the expansion of carbon capture projects based on this system.”
In a virtualized environment, whether deploying new processes or replicating or optimizing existing processes, it will become easier. With the powerful feature of reusable engineering, enterprises can greatly improve engineering efficiency, shorten project launch time, and stand out in the industry with significant advantages.
Actively embracing software defined automation and moving towards the future of industry
In the current era of continuous development and evolution of industrial automation technology, engineers and machine manufacturers are continuously innovating to improve enterprise efficiency, productivity, flexibility, and agility in response to the increasingly fierce market landscape. It is not difficult to see that leveraging the powerful capabilities of virtualization technology and creating software defined automated operational methods has become a necessary capability for enterprises to move towards the industrial future.
Industrial innovation is leading the arrival of the era of software defined automation. With the increasingly mature digital and virtualized intelligent manufacturing environment, it will undoubtedly continue to bring new interoperability, convenience, and efficiency standards, continuously promoting the development of industrial automation.
At the upcoming 2024 Hanover Industrial Expo, Schneider Electric will connect seven exhibition themes, including “Infrastructure, Chemical Industry, Industrial Water and Wastewater Treatment, Bioprocessing, Green Material Production, Packaging and Logistics, and Industrial Software”, with a nearly 2000 square meter large exhibition booth, to showcase the future industrial development landscape through software, automation, and electrification.
For more highlights, please stay tuned for the live broadcast of the Schneider Electric Hanover Industrial Expo booth on April 24th at 3:00 PM. Welcome to Schneider Electric’s video account to make an appointment to watch.
Warehouse stock recommendation:
IS200JPDEG1A
IS200VPROH1BEF
IS200VPROH2B
IS200VPROH2B
IS200VPWRH1AHD
IS200VPROH1BEF
IS200VPROH2B
IS420ESWBH3AX
IS220PDIAH1BE
IS220PDIAH1BE
More……