Description
IS210MVRBH1A – I/O Interface Board is available in stock which ships the same day.
IS210MVRBH1A – I/O Interface Board comes in UNUSED as well as REBUILT condition.
To avail our best deals for IS210MVRBH1A – I/O Interface Board, contact us and we will get back to you within 24 hours.
Functional Description
IS210MVRBH1A is an I/O interface board designed and developed by GE. It is a part of Mark VIe control system. The component includes a temperature sensor with an accuracy of 2 degrees Celsius. It is a specialized module designed to operate seamlessly within Mark systems, which are advanced control and monitoring systems. The module is commonly used in conjunction with the PMVE input-output pack, which further enhances its functionality and integration capabilities.When an excessive temperature is detected, a diagnostic alarm is generated, and the logic is stored in the database (signal space) to allow for additional control action or unique process alarm messages. Furthermore, the temperature is always available in the database. Because each I/O pack communicates directly on IONet, each I/O pack can be replaced independently without affecting any other I/O in the system. Furthermore, the I/O pack can be replaced without removing any field wiring.(https://www.weikunfadacai1.com/)
IS210MVRBH1A Features
R/S/T ADIO Interface: Specifically configured to interface with R/S/T ADIO (Analog/Digital Input/Output) devices. Handles both analog and digital signals for input and output operations.
Connectivity Facilitator: Acts as an intermediary to facilitate connectivity and interface within the control system. Enables communication, data exchange, and control between the module and other control system components.
Mark VIe Compatibility: Designed for seamless integration with the Mark VIe control system. Ensures compatibility for efficient data exchange and coordinated operation with other system modules.
Modular Design: Engineered with a modular approach for easy installation and removal. Simplifies maintenance, upgrades, and system expansion.
Protocol Alignment: Aligns with protocols and communication standards used in Mark systems. Reliable and efficient for control and data exchange.
PMVE Input-Output Pack Integration: When combined with the PMVE input-output pack, extends input and output capabilities. Manages a broader range of signals, sensors, and actuators for increased system versatility.
Unit Data Highway Communication: Utilizes the Unit Data Highway (UDH) communication protocol for high-speed, reliable data exchange within Mark system architecture.
Efficient Data Exchange and Control: Facilitates real-time data exchange and control commands with other modules and devices. Optimizes system performance and responsiveness.
Enhanced Data Handling: Capable of processing diverse data types and managing complex information. Manages sensors, actuators, and control signals effectively.
Reliable and Robust: Prioritizes reliability and robustness through rigorous quality testing. Maintains consistent and dependable performance even in challenging industrial environments.
Product Attributes
Compliance with industry standards: The board may comply with industry standards such as ISA S84 or IEC 61508, which specify requirements for the design, operation, and maintenance of safety instrumented systems in the process industry.
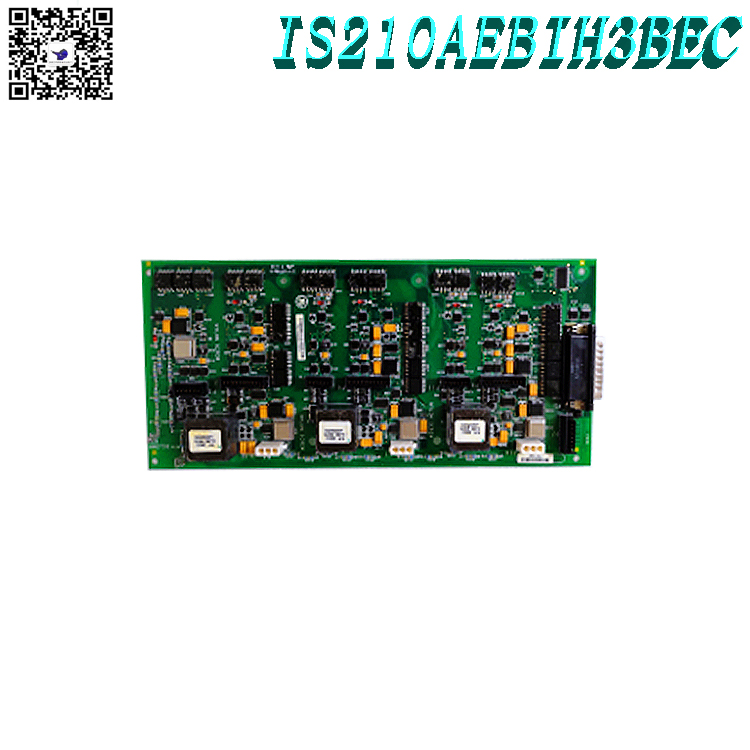
Fault detection and diagnostics: The board may have built-in capabilities for fault detection and diagnostics, which can help to identify and diagnose issues with the gas turbine control system.
Redundancy and fail-safe operation: The board may have redundancy and fail-safe operation features to ensure that the gas turbine control system continues to operate in the event of a failure or malfunction.
Compact design: The board may have a compact design that allows it to fit into tight spaces or enclosures.
System I/O Pack
The Mark VIe control system utilizes I/O packs consisting of a generic processor board and a data acquisition board specific to the type of connected device. These I/O packs play a crucial role in the digitization of signals, running algorithms, and facilitating communication between the connected devices and the Mark VIe controller.
One of the key functionalities of the I/O pack is fault detection. This is achieved through a combination of specialized circuitry within the data acquisition board and software running on the CPU board. By continuously monitoring the connected devices and analyzing the acquired data, the I/O pack can detect faults or abnormalities in the signals. The fault status is then communicated to the controllers, enabling appropriate actions to be taken.
For effective communication, the I/O pack is equipped with network interfaces that facilitate the transmission and reception of inputs and outputs. When both network interfaces are connected, the I/O pack ensures reliable data exchange between the connected devices and the controller.
.jpg)
Additionally, each I/O pack is capable of sending an identification message, known as an ID packet, to the main controller upon request. The ID packet contains important information about the I/O board, including its hardware catalog number, hardware revision, board barcode serial number, firmware catalog number, and firmware version. This information aids in system identification, tracking, and maintenance.
To ensure reliable operation in varying environmental conditions, the processor board and data acquisition board of the I/O pack are designed to operate within a temperature range of -30°C to 65°C. The convection cooling mechanism allows the I/O pack to dissipate heat effectively without the need for additional cooling mechanisms.
Temperature monitoring is also an integral part of the I/O pack’s functionality. Each I/O pack is equipped with a temperature sensor that provides accurate temperature readings with a precision of 3.6 degrees Fahrenheit. These temperature readings are stored in the system database and can be utilized to trigger alarms or notifications in case of temperature anomalies, allowing for proactive maintenance and preventing potential issues.
System Input Processing
In the Mark VIe control system, the handling of input data varies depending on the configuration and redundancy requirements. All three controllers in the system have access to all inputs, but the data is processed in different ways based on the specific scenario.
.jpg)
When there is only one I/O module with input signals, all three controllers utilize the same value as a common input without any voting process. In this case, the input signal is directly used by each controller without any comparison or decision-making.
Alternatively, the signals from all three I/O channels can be combined through a voting process to form a single input value. This is applicable when multiple sensors are providing input signals or when a single sensor’s output is distributed to multiple I/O channels using terminal board hardware fanning. By voting together, the system can evaluate the input signals from different sources and determine a single value to be used by the controllers. This voting mechanism can enhance redundancy and reliability in the input processing.
Furthermore, to simplify the configuration process, the Mark VIe control system offers a selection/voting/fault detection algorithm for input selection and voting. This algorithm is designed to be simple, highly reliable, and efficient, reducing the effort required for application configuration. It allows users to define the input selection criteria and voting rules based on their specific requirements. By utilizing this algorithm, the system maximizes the reliability options for a given set of sensor inputs and ensures compatibility with output voting mechanisms.
The Mark VIe control system provides flexibility in configuring the input processing options on a per-terminal-board basis. This means that for each terminal board in the system, all applicable subsets of reliability options are available. This flexibility allows users to tailor the input processing configuration to their specific needs and optimize the system’s reliability based on the application requirements.
In summary, the Mark VIe control system offers various input processing capabilities, including direct use of common inputs, voting of multiple input signals, and a configurable selection/voting/fault detection algorithm. These features maximize reliability options, provide redundancy, and ensure hardware compatibility with output voting mechanisms, allowing for a robust and customizable input processing solution for industrial applications.
System Features
The Mark VIe Distributed Control Solution incorporates a range of advanced features that enhance connectivity, performance, and lifecycle management. Its Ethernet-based distributed architecture serves as a foundation for these features, enabling secure and efficient communication between controllers and I/O devices. Here are the key system features:
Ethernet-Based Distributed Architecture: The Mark VIe system is built upon an Ethernet infrastructure, providing a reliable and scalable network for data transmission. This architecture enables seamless connectivity between controllers, I/O modules, and other networked devices. By leveraging Ethernet technology, the system ensures high-speed and secure communication throughout the control network.
Enhanced Performance: The Mark VIe system utilizes 100 MB Ethernet connectivity at all levels, enabling fast and efficient data exchange between controllers and I/O devices. This high bandwidth allows for rapid execution speeds of up to 40ms, ensuring real-time responsiveness and precise control in industrial processes. The improved performance of the system contributes to increased productivity and operational efficiency.
Simplified System Design: The use of secure peer-to-peer Ethernet connections between controllers and I/O simplifies the overall system design. By eliminating the need for complex and centralized communication architectures, the Mark VIe system streamlines the configuration and integration process. This simplification reduces implementation time and effort, making it easier to deploy and maintain the control solution.
Hot Swap Capabilities: The Mark VIe system incorporates hot swap capabilities, which enable system maintenance without requiring a system restart or configuration downloads. This means that individual components, such as controllers or I/O modules, can be replaced or updated while the system remains online and operational. Hot swapping enhances system availability and reduces downtime during maintenance activities, maximizing process continuity and plant uptime.(https://www.weikunfadacai1.com/)
Lifecycle Management: The Ethernet-based distributed architecture of the Mark VIe system facilitates efficient lifecycle management. It allows for seamless integration of new devices, upgrades, and expansions, ensuring the scalability and adaptability of the control solution as operational needs evolve over time. The system provides robust configuration management and version control, simplifying system updates and ensuring compatibility between different components.
I/O Pack Features
The Input/Output (I/O) pack, a critical component within a control system, plays a multifaceted role in maintaining system health and facilitating efficient data communication. Here, we delve into the key features and functions that make the I/O pack an indispensable part of the control system:
1. Comprehensive Fault Detection:
The I/O pack excels at fault detection through a synergistic combination of specialized hardware circuitry integrated into the data acquisition board and advanced software routines executed on the Central Processing Unit (CPU) board.
This cooperative approach ensures a robust method for identifying potential issues within the system, enhancing overall reliability.
2. Hardware and Software Integration:
At its core, the I/O pack’s fault detection mechanism relies on the close interaction between its hardware and software components.
The data acquisition board boasts sophisticated circuitry designed to continuously monitor signals and inputs from sensors and devices within the control system, swiftly identifying anomalies or deviations in incoming data.
3. Software-Driven Analysis:
The CPU board executes intricate software routines, purposefully designed to interpret data collected from connected sensors and devices.
Complex algorithms analyze this data, detecting patterns and comparing it against predefined thresholds or expected ranges. Any deviation or abnormality triggers an immediate alert or fault status.
4. Network-Wide Alerting:
Detected fault statuses aren’t confined to the I/O pack alone; they are efficiently transmitted to other system components, controllers, or monitoring systems within the control network.
Timely sharing of fault status information is critical for maintaining overall system health, as issues in one part of the system may have ripple effects on other connected components.
5. Data Handling and Communication Hub:
The I/O pack acts as a pivotal link within the control system’s communication network.
It manages the bidirectional flow of data, transmitting inputs from sensors and devices to central processing units and controllers while also receiving output commands from central units and relaying them to actuators and devices.
This seamless data exchange ensures that the control system operates cohesively and responds accurately to dynamic conditions.
6. Redundant Network Interfaces:
I/O pack offers the versatility to operate across multiple network interfaces.
In systems equipped with redundant network connections, the I/O pack actively communicates through both interfaces.
This redundancy enhances system reliability and fault tolerance, providing alternative communication paths. In the event of a disruption in one network interface, the other continues to transmit and receive data, assuring uninterrupted control system operation.
Plant Data Highway
The PDH (Peripheral Data Highway) serves as an optional interface that establishes connections between the CIMPLICITY* HMI/data server and various remote devices, including operator stations, printers, historians, and other customer computers. However, it’s important to note that the PDH does not establish a direct connection with the controller. Let’s explore the key details of the PDH, including its media, network architecture, and hardware components.
The communication media employed by the PDH can either be UTP (Unshielded Twisted Pair) or fiber-optic Ethernet. This media operates at a speed of 10/100 megabits per second, facilitating the transmission of data at high rates. These communication links utilize the TCP/IP protocol, a widely adopted standard for network communication, ensuring compatibility and seamless data exchange.
In certain system configurations, redundancy is a critical consideration. Redundant cables are a requirement for some systems that incorporate the PDH. These redundant cables are an integral part of a unified logical network, enhancing the reliability and fault tolerance of the overall communication infrastructure. Redundancy ensures that data flow remains uninterrupted, even in the presence of network disruptions.
The PDH hardware comprises two redundant Ethernet switches, which offer optional fiber-optic outputs for extended distances. This fiber-optic capability is particularly valuable when establishing connections to remote locations, such as a central control room. These redundant switches work in tandem to maintain network availability, further enhancing the system’s reliability.
On smaller systems, it’s worth noting that the PDH and the UDH (Universal Data Highway) may share the same physical network infrastructure. However, this coexistence is contingent on the absence of peer-to-peer control on the UDH. Careful network planning and configuration are essential to ensure seamless and efficient communication within the system.
Functional verification testing
We conducted functional verification testing on IS210MVRBH1A in actual OEM system settings. Due to the use of OEM systems, we can guarantee 100% reliability. Like any other card, all inputs and outputs will be individually validated for their functionality. Therefore, each channel is individually validated. According to the different types of circuit boards, we conduct load tests to ensure the appropriate stability of the circuit board.
Circuit board processing.
IS210MVRBH1A, like VME board, is an electrostatic sensitive board.
We suggest minimizing contact with PCBs, especially in conductive areas. If you need to hold them directly, please hold their edges. Always wear anti-static gloves. These devices require appropriate ESD safety precautions to be taken.
FREQUENTLY ASKED QUESTIONS
What is IS210MVRBH1A?
It is an I/O interface board developed by GE
What is the function of the I/O packs in the Mark VIe system?
Each terminal board’s I/O packs digitize the signal, run algorithms, and communicate with the Mark VIe controller. They detect faults by combining special circuitry in the data acquisition board with software running on the CPU board.
What is the temperature range of operation for the I/O packs?
The processor board and data acquisition board of the I/O pack are rated for -30°C to 65°C operation with free convection cooling.
How accurate is the temperature sensor in the I/O packs?
The temperature sensor in the I/O packs is accurate to 3.6 degrees Fahrenheit.
Can the temperature of the I/O packs be monitored?
Yes, each I/O pack temperature is stored in the database and can be used to trigger an alarm.
Popular model recommendations:
Reviews
There are no reviews yet.