Description
On/Off Windows Each counter has two configurable On/Off windows that compare the accumulated count or frequency of incoming pulses to user-defined On/Off values. When the count or frequency values are within the user-defined window parameters, the module sets the corresponding bit in the Counter[x].InWindow0 or Counter[x].InWindow1 input tag. The module produces data to the system on the rising and falling edge of each On/Off window. A rising edge occurs when a count or frequency value enters the window, and a falling edge occurs when a count or frequency value exits a window. You define each On/Off window by using these parameters: • Comparison method—Defines whether the On/Off window uses accumulated count, instantaneous frequency, or average frequency. You define the comparison method for a window on the Counter Configuration tab of the Module Properties dialog box.
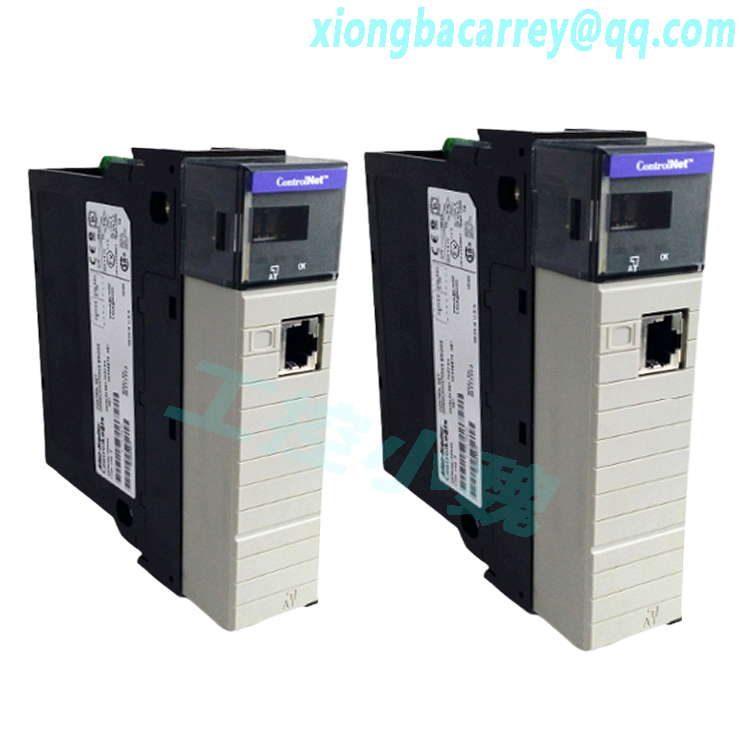
Figure 2 compares two On/Off windows by using the Accumulated Count comparison method. In the first window, the On value is less than the Off value. In the second window, the On value is greater than the Off value. Figure 2 – Window States Based on Accumulated Count The Counter[x].InWindow0 and Counter[x].InWindow1 input tags can be consumed by a controller or a 1756-OB16IEF peer output module and used to affect outputs. For more information about using peer modules, see the ControlLogix Peer I/O Control Application Technique, publication 1756-AT016. Rollover Values A rollover value determines how many counts accumulate before the count rolls over to zero. The count rolls over to zero on the rollover value. Each counter can have one rollover value.
.jpg)
For real-time control, you define a rollover value in the Counter[x].Rollover output tag. The following criteria applies to a rollover value: • The default rollover value is a maximum count of 231. • A rollover value must be a positive DINT value. If an invalid rollover value is defined, the module will use a value of 231. Counter[x].Window0On tag = 2000 Counter[x].Window0Off tag = 5000 Counter[x].InWindow0 turns On at count 2000. Counter[x].InWindow0 remains On for 3000 counts. Counter[x].InWindow0 turns Off at count 5000. On Value < Off Value Counter[x].Window1On = 5000 Counter[x].Window1Off = 2000 Counter[x].InWindow1 remains Off for 3000 counts. Counter[x].InWindow1 turns Off at count 2000. Counter[x].InWindow1 turns On at count 5000. On Value > Off Value E
The counter module provides four counter control functions: • Up/Down Count • Count Enable • Reset Count • Preset Count The module provides two methods to invoke counter control functions: • Hardware inputs—You can tie counter control functions to standard hardware inputs 0…7 to let the state of external input devices directly control the functionality of a designated counter. To configure this method, you use the Input Configuration tab within the module’s properties to set up ties as shown in Figure 3 on page 16. • Output tags—The output tag method enables you to programmatically control the counter functions via the module’s output tags. This method offers the most flexibility in invoking counter control functions. However, the response time is limited due to the time required for the controller to process your application routine. Keep in mind the following when tying hardware inputs to counter control functions: • A single input can control functionality for multiple counters. For example, you can tie input 3 to the Up/Down Count function for all eight counters. • Only one type of counter control function can be tied to a single input. For example, you cannot tie both the Count Enable and Reset Count functions to the same input. • If you do not require hardware inputs 0…7 to support counter control functionality, you can use the inputs as general purpose On/Off inputs without timestamping. Up/Down Count Function The Up/Down Count function causes a counter to increment or decrement accumulated count or changes the direction bit for frequency values. To invoke the Up/Down Count function for a counter by using the hardware input method, tie the function to a hardware input on the Input Configuration tab of the Module Properties dialog box as shown in Figure 3.When tied to a hardware input, this function is level-sensitive resulting in a change of status when the input is either low or high: • By default, counting starts only when the input is high and stops when the input is low. • When the function is inverted, counting starts only when the input is low and stops when the input is high. To invoke the Count Enable function by using the output tag method, use the Counter[x].DisableCount output tag as shown in Figure 7.
.jpg)
Key the removable terminal block (RTB) to prevent inadvertently connecting the wrong wiring in the RTB to your module. Wedge- and U-shaped bands are manually inserted into the RTB and module. This process hinders a wired RTB from being accidentally inserted into a module that does not match the positioning of the respective tabs. Key positions on the module that correspond to unkeyed positions on the RTB. For example, if you place a U-shaped keying band in slot 4 on the module, do not insert a wedge-shaped tab in slot 4 on the RTB, or your RTB will not mount on the module. We recommend that you use a unique keying pattern for each slot in the chassis. Follow these steps to key the RTB. 1. To key the module, insert the U-shaped band with the longer side near the terminals. 2. Push the band onto the module until it snaps into place.3. To key the RTB in positions that correspond to unkeyed module positions, insert the straight, wedge-shaped tab on the RTB with the rounded edge first. Each RTP comes with housing. Wire the RTB with a 3.2 mm (1/8 in.) maximum screwdriver before installing it onto the module. Cage Clamp Follow these steps to wire a cage clamp. 1. Strip 9.5 mm (3/8 in.) maximum length of wire. 2. Insert the wire into the open terminal on the side. 3. Turn the screw clockwise to close the terminal on the wire.The open section at the bottom of the RTB is called the strain relief area. The wiring from the connections can be grouped with a plastic tie. (1) The ControlLogix system has been agency certified using only the ControlLogix RTBs (1756-TBCH, 1756-TBNH, 1756-TBSH, and 1756-TBS6H). Any application that requires agency certification of the ControlLogix system using other wiring termination methods may require application specific approval by the certifying agency.
.jpg)
RTB Wiring Recommendations Consider these guidelines when wiring your RTB: • Begin wiring the RTB at the bottom terminals and move up. • Use a tie to secure the wires in the strain relief area of the RTB. • A jumper bar is shipped with certain I/O modules to assist in installation. Additional jumper bars can be purchased in packages of 25 by ordering catalog number 1756-JMPR. • For applications that require heavy gauge wiring, order and use an extended-depth housing, catalog number 1756-TBE. The following diagrams provide wiring examples for the eight counter, eight input point, 24V high-speed DC isolated, sink/source input module. For alternate wiring for use with non-IEC Type 3 sensors, refer to Appendix D.Exact Match Exact Match keying requires all keying attributes, that is, Vendor, Product Type, Product Code (catalog number), Major Revision, and Minor Revision, of the physical module and the module created in the software to match precisely to establish communication. If any attribute does not match precisely, I/O communication is not permitted with the module or with modules connected through it, as in the case of a communication module. Use Exact Match keying when you need the system to verify that the module revisions are exactly as specified in the project, such as for use in highly-regulated industries.
Model recommendation:
Reviews
There are no reviews yet.