Description
Many products have not been listed yet. For more products, please contact us
If the product model is inconsistent with the displayed image, the model shall prevail. Please contact us for specific product images, and we will arrange for photos to be taken and confirmed in the warehouse
We have 16 shared warehouses worldwide, so sometimes it may take several hours to accurately return to you. We apologize for any inconvenience caused. Of course, we will respond to your concerns as soon as possible.
PFVI102 Other names:
Input/output module PFVI102
PFVI102 log module
AI card PFVI102
Digital quantity module PFVI102
Get the competitive edge through the Millmate Roll Force System health check. Measurement made easy.Overview Millmate Roll Force System Health check is a detailed and comprehensive inspection and status evaluation of a roll force measurement installation. It is a key service to ensure and verify the actual roll force measurement accuracy to avoid future interruptions in the production. All findings are documented in a roll force system health check report and the recommendations can be used to secure measurement accuracy and availability, mill performance and yield. Features Check of: • Millmate Roll Force System Basics • Millmate Controller – Errors, warnings, alarms and info check – Software version • Matching unit(s) • Mechanical installation • Load cell insulation resistances • Recommended spares Benefits • Verifies the functionality of the roll force system and identifies shortcomings which might affect the measuring accuracy of the system • Secure roll force measurement performance availability, reliability and production yield • Minimizes risk of failures • Reduces mill maintenance costs.
Service duration Typically 1 day on-site to inspect the roll force measurement installation, evaluate and give recommendations if further actions are needed. During at least 4 hours, load cells and pressure plates need to be accessible outside the mill stand for inspection and testing. This can be done during a planned maintenance stop, or by the customer exchanging to spare load cells and spare pressure plates in the mill stand in advance. Additional time for travel, preparation, analysis and reporting is needed.
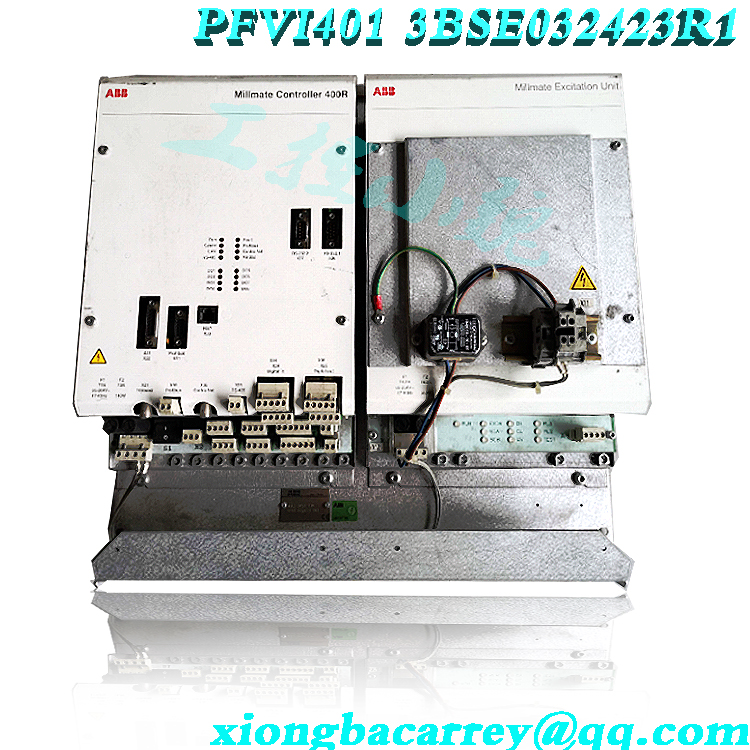
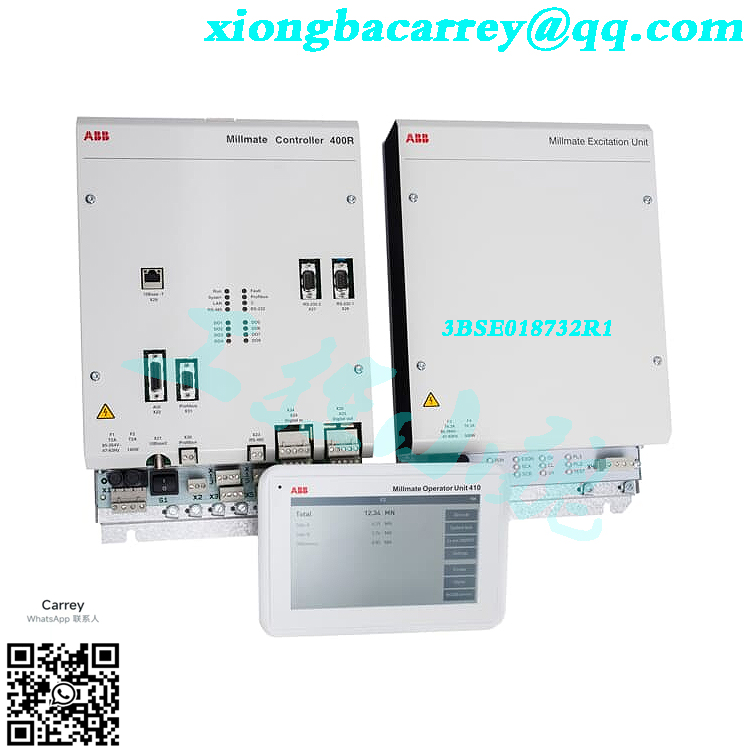
Your system for tension measurement consists of:
• Tension Electronics PFEA113
• Load cells of type PFCL 301E, PFTL 301E, PFRL 101, PFTL 101, PFCL 201 and PFTL 201
• Junction Box PFXC141
This advanced tension electronics can supply up to four load cells and has six configurable analog outputs for control and/or monitoring of web tension. The output signals are also available on Profibus-DP. Another useful feature is the possibility to, via the digital input or Profibus, switch the gain for two different web paths (gain scheduling) and zero set. This unit also includes a self-diagnostic function and four configurable digital outputs for alarms and level detection. Status of self-diagnostic functions are also available on Profibus-DP. By combining up to three PFEA113 the system can handle segmented roll applications, for example winders, with up to 12 load cells. The high level of functionality and user friendliness make the PFEA113 one of the most complete tension electronics on the market. Covering a wide range of applications the Tension Electronics comes in three versions (PFEA 111 and PFEA 112 are described in a separate manual), with different levels of performance and functionality. All three versions have multi-language digital display and configuration keys. The configuration keys being used for setting different parameters and to check the status of the tension system. The 2 x 16 character display can present sum, difference or individual load cell signals. All three versions are available in both DIN-rail version (IP 20-version, unsealed) and enclosed IP 65-version (NEMA 4) for mounting in more severe environments. The equipment is intended for use in a wide range of manufacturing processes where web material of any kind, e.g. paper, plastic or textile, is transported in a machine. The only requirement is that the web is wrapped over a roll. The force on the roll is proportional to the web tension. The resulting force is transferred through the bearing housings into the load cells. The load cells create a signal that is proportional to the force acting in the measuring direction of the load cells. This signal is processed and amplified in the tension electronics and can be used as an input signal for process control, presentation on a display or for registration.
Stressometer system in the hot rolling mill ”The hot Stressometer installation is running very well and we have really achieved better quality. The good tailout from the hot rolling mill results in high quality head-in to the cold rolling mill. Further, we have increased rolling speed and the yield is also better than before. We also got good hot mill strip flatness and benefit for cold rolling speed performance and quality.” Stressometer systems in the cold rolling mills ”The rolling mill performance is much better with the Stressometer flatness systems. We have increased the productivity step by step and the availability has improved a lot. The measurements are very stable and reliable and we have seen a considerable decrease of scrap due to the Stressometer installations. Further, in the long term we have increased the production speed from 300 m/min to 1500 m/min and thereby we have succeeded to increase our production efficiency considerably.” Millmate Thickness Gauging (MTG) in the cold rolling mills ”The accuracy is very good with the MTG-gauges. Further, MTG-gauges are alloyindependent and for the clad mode, the measurement is insensitive to the alloy chemistry. We see a big advantage with the noncontact MTG thickness gauges having very stable and reliable measurements over time. Also, there is a minimum of maintenance and there are no radiation problems with MTG.”
.jpg)
All products on this website are special products, and market prices have been fluctuating,
The specific customer service quotation shall prevail, as the product is a new product and the price is not genuine,
Please confirm the model, product, price, and other detailed information with customer service before placing an order. The website has been used,
The new one is for sale, please contact customer service to communicate.
Model recommendation:
PFVI401 3BSE018732R1
PFVI401
PFVI401 3BSE032423R1
3BSE024387R4
PFCA401SF
PFCA401SF 3BSE024387R4
PFEA111-IP65
3BSE024388R4
PFXA401SF
PFXA401SF 3BSE024388R4
HIEE400995R0002
More……
Reviews
There are no reviews yet.