Description
Get the competitive edge through the Millmate Roll Force System health check. Measurement made easy.Overview Millmate Roll Force System Health check is a detailed and comprehensive inspection and status evaluation of a roll force measurement installation. It is a key service to ensure and verify the actual roll force measurement accuracy to avoid future interruptions in the production. All findings are documented in a roll force system health check report and the recommendations can be used to secure measurement accuracy and availability, mill performance and yield. Features Check of: • Millmate Roll Force System Basics • Millmate Controller – Errors, warnings, alarms and info check – Software version • Matching unit(s) • Mechanical installation • Load cell insulation resistances • Recommended spares Benefits • Verifies the functionality of the roll force system and identifies shortcomings which might affect the measuring accuracy of the system • Secure roll force measurement performance availability, reliability and production yield • Minimizes risk of failures • Reduces mill maintenance costs(https://www.weikunfadacai1.com/)
Service duration Typically 1 day on-site to inspect the roll force measurement installation, evaluate and give recommendations if further actions are needed. During at least 4 hours, load cells and pressure plates need to be accessible outside the mill stand for inspection and testing. This can be done during a planned maintenance stop, or by the customer exchanging to spare load cells and spare pressure plates in the mill stand in advance. Additional time for travel, preparation, analysis and reporting is needed.
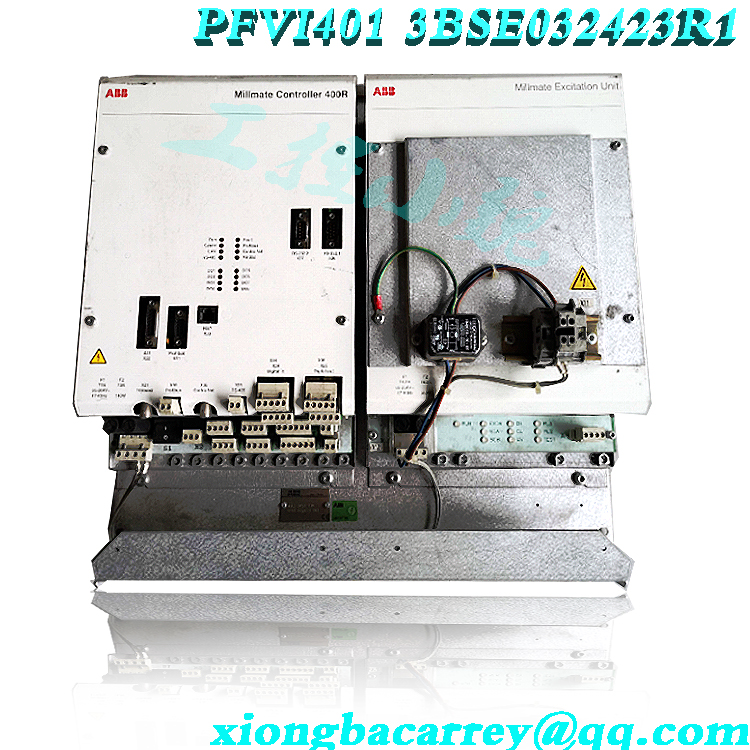
Note: Free access to the mechanical parts and the mounting surfaces in the actual mechanical installation is essential for achieving the expected goals with the Health Check during the site visit. The accessible parts required for different load cell types and positions in the mill stand are listed below. Installations with rectangular load cells below the lower back up roll or above the upper back up roll: Accessible parts: Mounting surfaces in the mill stand, the sledges if present, the rockers, the pressure plates closest to the load cells and intermediate mating plates if present. Installations with circular load cells under the screw-down or hydraulic cylinder: Accessible parts: Mounting surfaces above the upper back up roll bearing chuck, plain or tapered thrust roller bearings, pressure plates closest to the load cells and other intermediate mating plates if present. Installations with annular load cells above the screw-down inside the mill stand: Accessible parts: Mounting surfaces of the screw-down nut, plain or tapered thrust roller bearings, pressure plates closest to the load cells. The parts and mounting surfaces mentioned above need to be accessible before the start of the work or otherwise the investigation of them need to be planned for in advance so that it can be performed later during the site visit
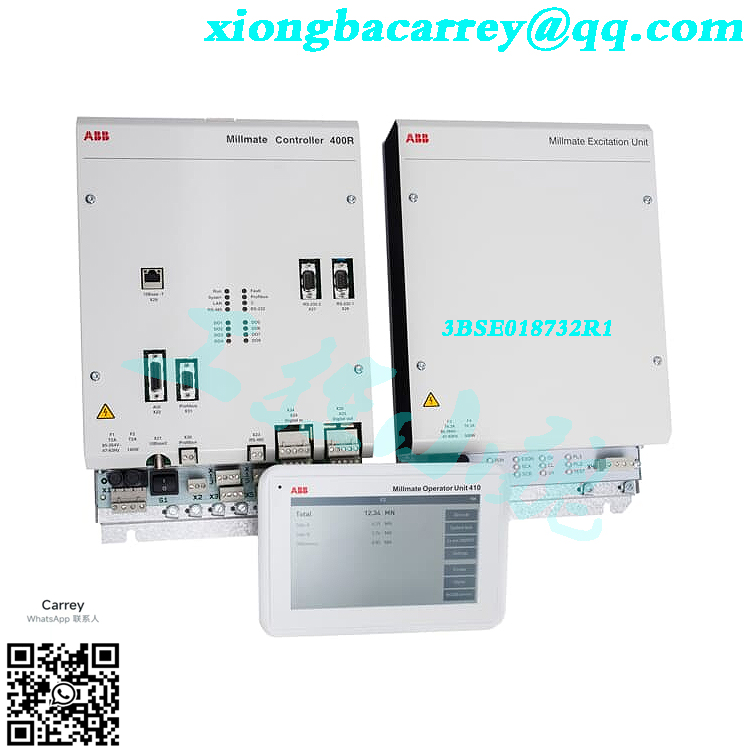
Note: Free access to the mechanical parts and the mounting surfaces in the actual mechanical installation is essential for achieving the expected goals with the Health Check during the site visit. The accessible parts required for different load cell types and positions in the mill stand are listed below. Installations with rectangular load cells below the lower back up roll or above the upper back up roll: Accessible parts: Mounting surfaces in the mill stand, the sledges if present, the rockers, the pressure plates closest to the load cells and intermediate mating plates if present. Installations with circular load cells under the screw-down or hydraulic cylinder: Accessible parts: Mounting surfaces above the upper back up roll bearing chuck, plain or tapered thrust roller bearings, pressure plates closest to the load cells and other intermediate mating plates if present. Installations with annular load cells above the screw-down inside the mill stand: Accessible parts: Mounting surfaces of the screw-down nut, plain or tapered thrust roller bearings, pressure plates closest to the load cells. The parts and mounting surfaces mentioned above need to be accessible before the start of the work or otherwise the investigation of them need to be planned for in advance so that it can be performed later during the site visit
Your system for tension measurement consists of:
• Tension Electronics PFEA113
• Load cells of type PFCL 301E, PFTL 301E, PFRL 101, PFTL 101, PFCL 201 and PFTL 201
• Junction Box PFXC141
This advanced tension electronics can supply up to four load cells and has six configurable analog outputs for control and/or monitoring of web tension. The output signals are also available on Profibus-DP. Another useful feature is the possibility to, via the digital input or Profibus, switch the gain for two different web paths (gain scheduling) and zero set. This unit also includes a self-diagnostic function and four configurable digital outputs for alarms and level detection. Status of self-diagnostic functions are also available on Profibus-DP. By combining up to three PFEA113 the system can handle segmented roll applications, for example winders, with up to 12 load cells. The high level of functionality and user friendliness make the PFEA113 one of the most complete tension electronics on the market. Covering a wide range of applications the Tension Electronics comes in three versions (PFEA 111 and PFEA 112 are described in a separate manual), with different levels of performance and functionality. All three versions have multi-language digital display and configuration keys. The configuration keys being used for setting different parameters and to check the status of the tension system. The 2 x 16 character display can present sum, difference or individual load cell signals. All three versions are available in both DIN-rail version (IP 20-version, unsealed) and enclosed IP 65-version (NEMA 4) for mounting in more severe environments. The equipment is intended for use in a wide range of manufacturing processes where web material of any kind, e.g. paper, plastic or textile, is transported in a machine. The only requirement is that the web is wrapped over a roll. The force on the roll is proportional to the web tension. The resulting force is transferred through the bearing housings into the load cells. The load cells create a signal that is proportional to the force acting in the measuring direction of the load cells. This signal is processed and amplified in the tension electronics and can be used as an input signal for process control, presentation on a display or for registration.
Stressometer system in the hot rolling mill ”The hot Stressometer installation is running very well and we have really achieved better quality. The good tailout from the hot rolling mill results in high quality head-in to the cold rolling mill. Further, we have increased rolling speed and the yield is also better than before. We also got good hot mill strip flatness and benefit for cold rolling speed performance and quality.” Stressometer systems in the cold rolling mills ”The rolling mill performance is much better with the Stressometer flatness systems. We have increased the productivity step by step and the availability has improved a lot. The measurements are very stable and reliable and we have seen a considerable decrease of scrap due to the Stressometer installations. Further, in the long term we have increased the production speed from 300 m/min to 1500 m/min and thereby we have succeeded to increase our production efficiency considerably.” Millmate Thickness Gauging (MTG) in the cold rolling mills ”The accuracy is very good with the MTG-gauges. Further, MTG-gauges are alloyindependent and for the clad mode, the measurement is insensitive to the alloy chemistry. We see a big advantage with the noncontact MTG thickness gauges having very stable and reliable measurements over time. Also, there is a minimum of maintenance and there are no radiation problems with MTG.”
.jpg)
Millmate Strip Scanner systems in the cold rolling mills ”The Millmate Strip Scanner system (MSS) is always working and the MSSsensors have been running perfectly for many years of operation. There is no maintenance and maintenance costs with MSS. MSS is very reliable as the sensor is unaffected by mill environment and the measurements are very stable. Coiler centering is very good with MSS. Also excellent recoiling without imperfections such as telescoping.” Large PillowBlock Tensiometers (LPBT) in the cold rolling mills ”Tension control is one of the most important process parameters in a process line. In order to achieve good tension control you need reliable input of the actual tension. Therefore the selection of reliable tension load cells is crucial. For Gränges the choice was ABB’s Large PillowBlock Tensiometers and the underlying Pressductor® technology. We appreciate the reliable and accurate measurements with ABB’s Large PillowBlock Tensiometers.” Pressductor Radial Tensiometers (PRT) in the cold rolling mills and process lines For measuring tension with shaftmounted load cells, PRT system is a highquality system that provides exceptional and long-lasting performance. PRT load cells and tension electronics are designed for medium-tension and light-tension process lines used in light gauge and loop slitters. Easy to install and virtually maintenancefree, PRT tension measurement makes a significant contribution to more productive operations and improvements in product quality.
[Service contact information]
Tel: 18030177759 (WeChat with the same number)
WhatsApp:+86 18030177759
QQ:2797820256
E-mail: xiongbacarrey@qq.com
Website: https://www.weikunfadacai1.com
Address: Unit 2009, 20/F, 1733 Luling Road, Siming District, Xiamen
Shipment: EMS, DHL, UPS and FEDEX
Payment method: telegraphic transfer
Supply capacity: 30 sets/set per month
Price: the more orders, the lower the price
Delivery: inventory, delivery within 3 days
Address: Unit 2009, Innovation Center, 1733 Lvling Road, Siming District, Xiamen
① 24 hours email reply (12 hours);
③ For goods shipped to countries outside Asia, please contact the Seller.
Xiamen Xiongba E-commerce Co., Ltd. main brand;
ABB GE
bentley Woodward
FOXBORO
WESTINGHOUSE Schneider
AB Motorola
GE EMERSON
YOKOGAWA Honeywell
EPRO ICS TRIPLEX
It is mainly used as the card driver of the spare parts module for the four major systems of PLC DCS robot servo
1. For inventory items, we will ship them to you within 3 days after receiving payment
2. We can ship goods to all parts of the world through DHL, UPS, FEDEX, TNT and EMS.
3. If you have a freight forwarder, please inform us before shipment.
4. We will pack the parts in strong boxes. If you have any special needs, please inform us.
5. We usually deliver the goods before 4:30 p.m., and we will send the tracking number to you after delivery. It takes 7-15 days to receive the package.
6. Please email us after receiving the package.
7. Please include all information when inquiring about the transportation cost, otherwise it will slow down the process.
8. What is your postal code?
9. If you have a company name, what is your company name?
10. If you have a telephone number and extension number, what is your telephone number?
11. We are the largest supplier in the region. We have great advantages in all kinds of popular and discontinued models. If you have models and spare parts that you can’t find
here, you can boldly send me to help you check!!!!!!
12. We only make spare parts for high-voltage and medium-high voltage products!!!!!!!
Model recommendation:
Reviews
There are no reviews yet.