Description
Indicators, control elements, diagnosis
The PacDrive™ System supports the user with its comprehensive diagnostic sys‐ tem. The diagnostic messages can be read out with the Automation Toolkit EPAS-4 or in the PD-Diagnostic. The PacDrive™ System contains a powerful message logger in which additional diagnostic information is recorded. Diagnostic messages are usually displayed on a control panel on the machine. If an ”error” occurs, read the diagnostic message on this unit and then contact the machine manufacturer. Detailed information on diagnosis is available in the Online-Help of the Automation Toolkit EPAS-4 or in the PD-Diagnostic.(https://www.weikunfadacai1.com/)
Indicators on the PacDrive C400 controller
If the cover of the Controller is closed, you will see four vertically arranged indicators, which signify various operating states or errors. pow (control voltage indicator) wd (watchdog indicator) err (error display) bus err (SERCOS real-time bus error indicator) In addition to the LED displays, further information about the operating status of the controller is given on the 4-line LCD display.
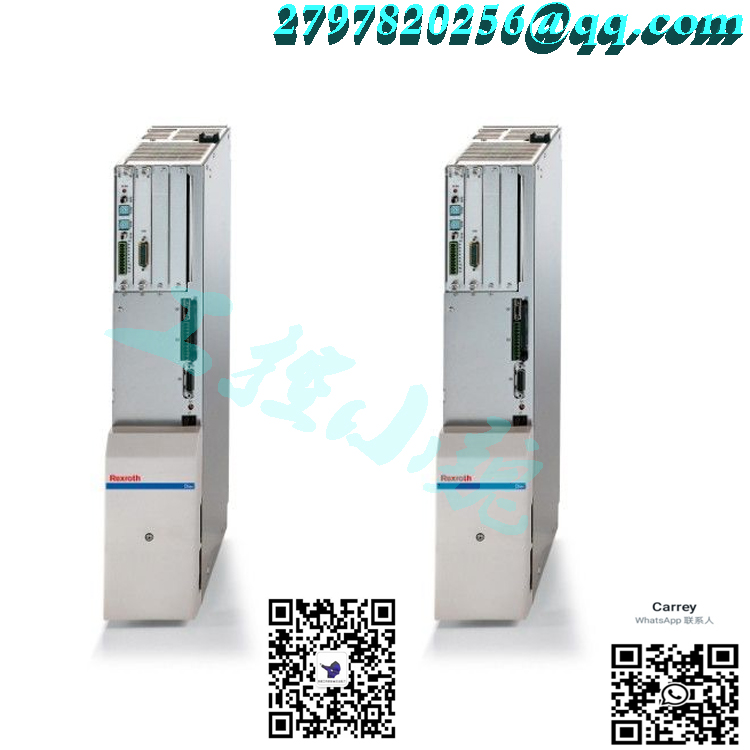
The horizontally arranged buttons on the controller currently have no function. Display during the boot with empty battery pack (UPS). Press the right button below the display to continue the boot and to start charging the battery pack.(https://www.weikunfadacai1.com/)
The err-LED is switched on following “Power on”. Once the operating system, user configuration, user parameters and the IEC program have been loaded and the IEC program has been started successfully the err LED will switch off again. The boot procedure is now complete.
.jpg)
The innovative iSH combines motor, final stages and the digital servo regulator for one axis in a space-saving housing. The sending power (fiber optic cable intensity) is set on the controller in the PLC configuration.
CompactFlashTM card slot
The CompactFlash™ card slot is the receptacle for the permanent data storage (CF™ card) of the controller. How to replace the Compact Flash™ in case of servicing:
Switch off controller.
Hold the CF™ card with your thumb and forefinger and pull it out of the slot.
To insert, carefully place the CF™ card on the guide rail and push it into the device.
Push lightly until the card clicks in.
Battery compartment
The controller battery buffers controller data (Bios, NVRAM, time, etc.).
Maintenance
interval The battery should be replaced every 6 years. After this period of time the battery must be replaced. If the device (with battery inserted) is not used for an extended period of time, you should check/replace the battery. Measurement This is how you measure the battery: Replace battery and continue with the manual measurement or observe the diagnostic message “037 Battery down“ in the IEC program and dis‐ play it on an HMI (panel), if necessary. Replace battery three days after the first diagnostic message at the latest. This is how you replace the battery: You can change the battery while the controller is on or off. There is no loss of data when it is performed with the controller on. When the controller is switched off, the time period allotted for data buffering without a battery is approx. 5 minutes.
A: There may be jam due to obstacles while placing bottles, …
So, if the gripper of the robot meets an obstacle while placing the bottles into the carton, the servo will deviate from its schedule. This deviation can be found by exam‐ ining Following Error. If Following Error exceeds the given limit dramatically, there should be a reaction –for example, stopping the movement of the gripper immediately if still possible to minimize damage of bottles, cartons or mechanics. After a timeout, PositionControl will be switched off. If Following Error exceeds Following Limit ‘slightly’, there should be a message but there is no need for a reaction of the ‘reporting’ drive. The message is worth the trouble, for • programmers will use it as a criterion to launch userspecific reactions of the ma‐ chine within the userprogram, • maintenance staff can gather these messages from the message logger and use them e.g. for ‘preventive maintenance’!
.jpg)
B: There may be friction due to fouling, worn out bearings, damaged mechanics, …
Friction requires ‘more than the usual amount of torque’ for a given movement or for cyclic sequences of them. Remedying this error is a bit more complex. For most of all cases, friction within an installation is not that obvious, that it immediately disturbs the schedule like the above obstacles did. Friction ‘kills’ the ServoDrive in the long run. Thus the MotorController takes root mean square of torque – determined via root mean current- to detect this kind of ‘continuous overload’. … and this is what we have come to know as ‘I2t’ in the previous lesson! The above ‘warning-philosophy’ applies again: If the drive is still functional and ‘I2t’ exceeds a certain threshold, there will be only a warning, either to be used as criteria for stopping the machine in a defined way on behalf of the userprogram, or as a message to be logged in the sense of preventive maintenance. If ‘I2t’ reaches its upper limit, the current movement will be stopped immediately and PositionControl will be switched off after the timeout mentioned above!
C, D: Sealing movements may require more than admitted effective current due to ‚exaggerated‘ cycle rate! The motion-profiles for the up-down-movement and the back and forth movement of the sealing-bar require acceleration- and deceleration-phases due to changing direc‐ tions. Increasing cycle rate will require more and steeper(!) accel- and decel-phases per cycle and that will result in rising the effective values of torque and current! This continuous overload will be detected and invoke a reaction in order to prevent overheating the Motor or the MotorController above their acceptable temperature ranges!
Model recommendation:
SAIA PCD3.W310 DIGITAL ANALOG INPUT CONTROL MODULE
METSO AI card A413331
METSO AI card A413188
BERGER LAHR stepper motor WPM311.03400
Reviews
There are no reviews yet.