Description
Many products have not been listed yet. For more products, please contact us
If the product model is inconsistent with the displayed image, the model shall prevail. Please contact us for specific product images, and we will arrange for photos to be taken and confirmed in the warehouse
We have 16 shared warehouses worldwide, so sometimes it may take several hours to accurately return to you. We apologize for any inconvenience caused. Of course, we will respond to your concerns as soon as possible.
Large hollow shaft with flange mounting
FHA-C Series Hollow Shaft Servo Actuators combine a synchronous servo motor, CSD Series Component Set, feedback sensor and a specially developed output bearing. Available in four sizes with gear ratios of 50, 100 and 160:1, the actuators can provide maximum torques from 39 to 823 Nm. The output bearing with high tilting capacity often allows direct attachment of heavy payloads without the need for further support, thereby providing simple and space saving design installations. To adapt to your specific application, the FHA-C Series offers many possible combinations when selecting the motor winding, motor feedback, brake, various sensors and cable as well as connector options. The integrated hollow shaft can be used to feed through supply lines or services for additional axes, enabling space saving designs with minimal installation dimensions required. The accurate positioning of the actuator ensures stable machine characteristics, lower rejection rates and consistent quality. By combining the FHA-C Actuators with the specially adapted YukonDrive® Servo Controllers, it is possible to provide a single source supply for a pre-configured drive system tailored to suit your application. Alternatively, the flexible configuration of the actuator ensures compatibility with almost any servo controller on the market.
Output Bearing
FHA series AC hollow shaft Servo Actuators incorporate a high stiffness cross roller bearing to support output loads. This specially developed bearing can withstand high axial and radial forces as well as high tilting moments. The reduction gear is thus protected from external loads, so guaranteeing a long life and consistent performance. The integration of an output bearing also serves to reduce subsequent design and production costs, by removing the need for an additional output bearing in many applications. Furthermore, installation and assembly of the FHA servo actuators are greatly simplified.https://www.weikunfadacai1.com/
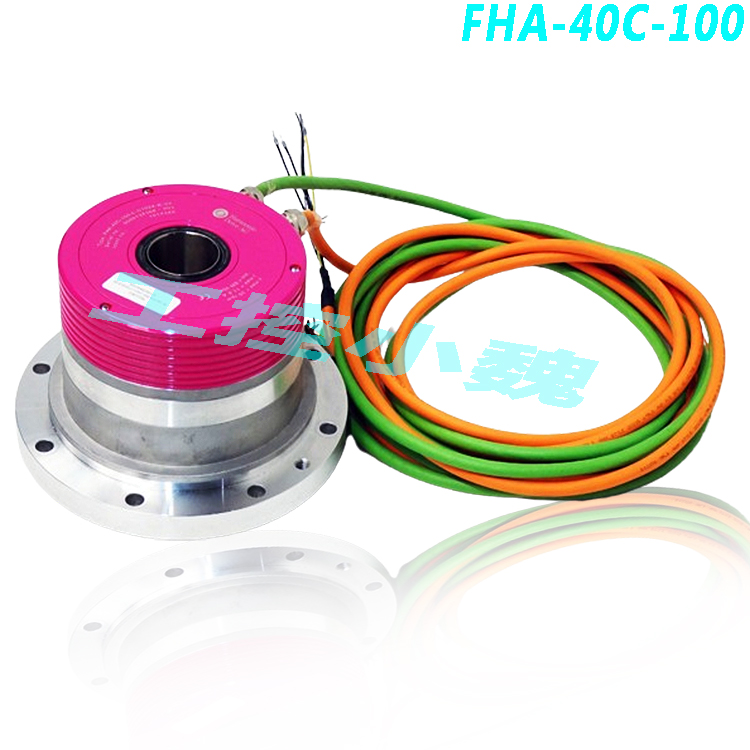
Design and Operation
For accurate position setting, the servo motor and its control device are fitted with a measuring device (feedback), which determines the current position (e.g. the angle of rotation set for a starting position) of the motor. This measurement is effected via a rotary encoder, e.g. a resolver, an incremental encoder or an absolute encoder. The position controller compares the signal from this encoder with the pre-set position value. If there is any deviation, then the motor is turned in the direction which represents a shorter path to the set value which leads to the deviation being reduced. The procedure repeats itself until the value lies incrementally or approximately within the tolerance limits. Alternatively, the motor position can also be digitally recorded and compared by computer to a set value. Servo motors and actuators from Harmonic Drive AG use various motor feedback systems which are used as position transducers to fulfil several requirements
.jpg)
Commutation
Commutation signals or absolute position values provide the necessary information about the rotor position, in order to guarantee correct commutation.
Actual Speed
The actual speed is obtained in the servo controller suing the feedback signal, from the cyclical change in position information.
Actual Position
Incremental encoder
The actual signal value needed for setting the position is formed by adding up the incremental position changes. Where incremental encoders have square wave signals, definition of the edge evaluation can be quadrupled (quad counting). Where incremental encoders have SIN / COS signals, then the definition can be increased by interpolation in the control device.
Absolute encoder
Absolute encoders deliver absolute position information about one (single turn) or several (multi-turn) rotations. This information can on the one hand provide the rotor position for commutation and on the other hand possibly a reference of travel. Where absolute encoders have additional incremental signals, then typically the absolute position information can be read at power up and the incremental signals then evaluated to determine the rotation and actual position value. Fully digital absolute encoders as motor feedback systems have such a high definition of the absolute value that there is no need for additional incremental signals.
.jpg)
Resolution
In conjunction with the Harmonic Drive AG high precision gears, the output side position can be recorded via the motor feedback system without any additional angle encoders having to be used. The resolution of the motor feedback system can also be multiplied by gear ratio.
Output Side Angle Measurement Devices
Where applications place higher demands on accuracy or need torsion compensation at high torque load, the FHA-C Series Actuators can be fitted with absolute measurement encoders directly to the actuator output (Option EC).
Protection against Corrosion and Penetration of Liquids and Debris
The product is fully protected provided that the connectors are correctly attached. Corrosion from the ambient atmosphere (condensation, liquids and gases) at the running surface of the output shaft seal is prevented. Contact between sharp edged or abrasive objects (cutting chips, splinters, metallic or minerals dusts etc) and the output shaft seal must be prevented. Permanent contact between the output shaft seal and a permanent liquid covering should also be prevented. A change in the operating temperature of a completely sealed actuator can lead to a pressure differential between the outside and the inside temperature of the actuator. This can cause any liquid covering the output shaft seal to be drawn into the housing which could cause corrosive damage. As a countermeasure, we recommend the use of an additional shaft seal (to be provided by the user) or the maintenance of a constant pressure inside the actuator.
Recommended servo drive models:
Reviews
There are no reviews yet.