Description
Product Description
8200-1302 is one of the various Woodward 505 digital governors that can be used to control steam turbines. This operator control panel serves as a graphical interface and keyboard, allowing adjustments to the turbine and communication with the turbine. This can be configured through the Modbus communication port on the device.
8200-1302 has multiple available functions:
Automatic start sequence for hot and cold starts, with temperature input options
Critical speed avoidance on the three speed belt
Ten external alarm inputs
Ten external DI trip inputs
Trip indication for tripping and alarm events with relevant RTC timestamps
Dual speed and load dynamics
Peak speed indication for overspeed tripping
Zero speed detection
Remote droop
Frequency Deadband
The device also provides three normal operating modes, including configuration, operation, and calibration modes.
This device includes two redundant speed inputs and can accept magnetic pickup devices, eddy current probes, or proximity probes. It has analog inputs (8) and can be configured for any of 27 functions. The device also has an additional 20 contact inputs. The first four of these contacts are used by default for closing, raising speed settings, resetting, and lowering speed settings. Other options can be configured as needed. In addition, the device also has two 4-20 mA control outputs and eight C-type relay contact outputs.
The front panel of 8200-1302 includes emergency trip keys, backspace/delete keys, Shift keys, as well as view, mode, ESC, and Home keys. It also has navigation cross keys, soft key commands, and four LEDs for correlating control and hardware status.
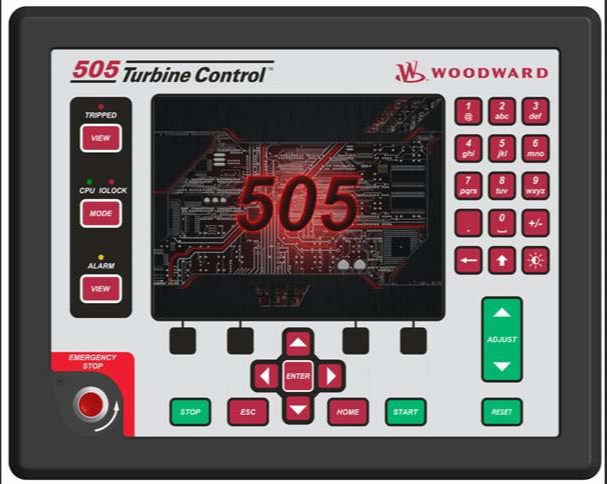
For more information on the use and installation of 8200-1302, please refer to Woodward’s original documentation.
The next generation 505D front panel is equipped with user configurable digital governor control for steam turbines, featuring an advanced integrated multilingual interface HMI screen. The new 505D is based on a powerful and reliable standard-setting 505 platform, now globally trusted, with extended communication protocols, intelligent/adaptive control algorithms, and advanced service tools with data logging and RemoteView monitoring capabilities. This model is a low-voltage 18-36 Vdc power input, rated for use in ships and ATEX Zone 2 hazardous locations.
Integrated graphics front panel HMI screen
Multi language screen, including Chinese, for easy operator use, diagnosis, and control
Large screen for easy navigation and icon viewing of parameters and performance
Operators and engineers can view real-time trends locally
Configurable label names for easy identification of connections
Internal “turbine simulator” for offline training and pre testing before system changes
Improving communication
Ethernet communication for connecting factory DCS, service tools, and RemoteView operator control panels
CANOpen actuator connection for Woodward VariStroke actuators and DSLC-II power management network
Intelligent/adaptive control algorithm
Next generation advanced load shedding performance
3 critical speed avoidance zones
Reverse sensing and alarm
OptiTune adaptive PID technology enables optimal setting of turbine performance
Accelerated PID can limit overshoot and achieve stable and efficient factory startup
High speed data log for monitoring turbine operation and pressure, including operating time and first out travel information
Vibration monitoring for protection and control (sensor kit 8928-7482)
Improved services/user tools
Network compatible password enable login
The RemoteView (8928-5311) program can perform virtual monitoring and control from remote workstations or mobile devices
The Control Assistant service tool can easily configure, save, compare, and view settings and data logs
Upgrade the existing 505 traditional steam turbine governor control device directly with product number 9907-164.
Use our convenient old 505 to new 505D modification wiring kit 5404-1801.
Flex500 is a programmable real-time, deterministic, dedicated digital controller that optimizes the performance and protection of compressors, steam turbines, gas turbines, and water turbines. Woodward is designed and built on our reliable, on-site validated 505D hardware platform, as well as our industry trusted and easy-to-use GAP program and advanced service tools. This model is rear panel mounted and suitable for ATEX and ship applications as well as hazardous rated locations with low voltage (18-36 Vdc) power inputs.
The Flex500 control system represents a new generation of dedicated controllers with optional RemoteView virtual terminal connections. This industrial hardware platform provides powerful and low-cost control for various turbine, engine, and compressor applications. Flex500 is a low-cost alternative to general-purpose PLCs, providing a simple, user-friendly GAP programming architecture and a true industrial production and support lifecycle, eliminating frequent high cost obsolescence issues.
The platform’s real-time operating system and dedicated inputs and outputs provide deterministic performance for key prime mover control functions. Its fast I/O scanning time, high accuracy, and software program synchronization make it an ideal choice for controlling and protecting critical high-speed rotating equipment.
Application:
Compressor Control and Protection
steam turbine
gas turbine
Hydraulic turbine
Gas and diesel engines
Features:
The rear panel has optional RemoteView virtual terminal connections
Powerful real-time microprocessor control
Fast and accurate onboard I/O channels
Combining real-time control with PLC programming
The deterministic I/O scan rate is as fast as 5 milliseconds.
Distributed I/O RTCnet ™ And LINKnet HT ™ compatible
Compliant with time synchronization protocol SNTP
Network control connection with DCS
Low cost alternative solutions for general PLC
Sulfur resistant conformal coating
Certified to standards or hazardous locations
Distributed Control System (DCS) System
Woodward based RTCnet ™ The and/or LINKnet HT distributed I/O module is designed as a distributed control system that can be used in conjunction with the Flex500 platform to expand the number and type of input and output signals according to specific application needs.
Ethernet, serial, and CAN communication ports, as well as related Modbus ® The TCP/IP and CANopen protocols also make this platform very suitable as a part of the entire factory DCS or as an independent controller. Four Ethernet ports and four CAN ports can achieve the network flexibility and redundancy required for today’s critical control system architecture.
Model recommendation:
Reviews
There are no reviews yet.